Clamping cartridge polymer pole ear welding method
A tab welding and polymer technology, applied in welding equipment, non-electric welding equipment, electrical components, etc., can solve the problems of difficult welding positioning, many working steps, slow welding speed, etc., to achieve easy positioning, fewer operation steps, Easy-to-use effects
- Summary
- Abstract
- Description
- Claims
- Application Information
AI Technical Summary
Problems solved by technology
Method used
Image
Examples
Embodiment Construction
[0024] See Figures 6 to 9:
[0025] Polymer tab welding method, the method comprises the following steps:
[0026] a. Cut the length of the lug according to the process requirements;
[0027] b. Place the negative tab 6 in the middle of the copper foil 5 corresponding to the cell, and align the upper edge 4 of the sealing film and the diaphragm;
[0028] c. Move to the ultrasonic welding machine, press down the battery so that the upper plane of the battery is level with the welding seat of the ultrasonic welding machine, and perform welding;
[0029] d, place the positive tab 7 in the middle of the aluminum foil 8 corresponding to the cell, and align the upper edge 4 of the sealing film and the diaphragm;
[0030] e. Move to the ultrasonic welding machine, press down the battery so that the upper plane of the battery is level with the welding seat of the ultrasonic welding machine, and perform welding;
[0031] f, cut off excess copper foil and aluminum foil;
[0032] g. ...
PUM
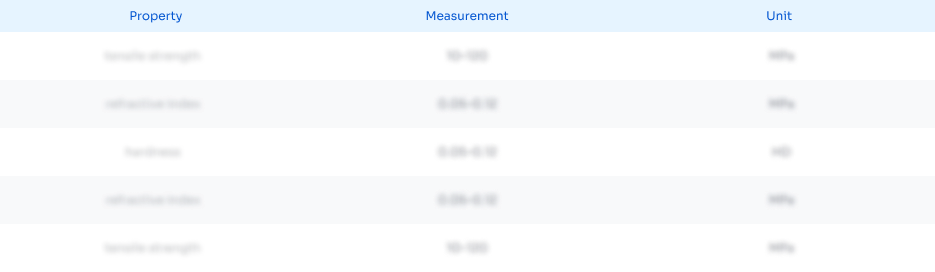
Abstract
Description
Claims
Application Information

- Generate Ideas
- Intellectual Property
- Life Sciences
- Materials
- Tech Scout
- Unparalleled Data Quality
- Higher Quality Content
- 60% Fewer Hallucinations
Browse by: Latest US Patents, China's latest patents, Technical Efficacy Thesaurus, Application Domain, Technology Topic, Popular Technical Reports.
© 2025 PatSnap. All rights reserved.Legal|Privacy policy|Modern Slavery Act Transparency Statement|Sitemap|About US| Contact US: help@patsnap.com