Low no-load-loss medium-frequency coreless induction furnace
An induction electric furnace and intermediate frequency technology, which is applied in the field of improved intermediate frequency coreless induction electric furnaces, can solve the problems of large no-load loss, complex yoke manufacturing process, and large no-load loss of electric furnaces, so as to reduce no-load loss and improve the utilization of electric energy. efficiency, and the effect of improving the efficiency of the electric furnace
- Summary
- Abstract
- Description
- Claims
- Application Information
AI Technical Summary
Problems solved by technology
Method used
Image
Examples
Embodiment Construction
[0018] The present invention will be further described in conjunction with the accompanying drawings of the above-mentioned embodiments.
[0019] As shown in the figure, the low-no-load loss intermediate frequency coreless induction furnace of the present invention includes a furnace shell, a melting chamber lining 7 and an induction coil 6, and the induction coil 6 is placed between the melting chamber lining 7 and the furnace shell 2. The outer side of the induction coil 6 is equipped with a magnetic conduction column 3, and the upper and lower ends of the magnetic conduction column 3 are respectively connected to the furnace mouth magnetic shielding plate 9 and the furnace bottom magnetic shielding plate 5. The cross section of the magnetic conduction column 3 is fan-shaped, and its inner side Corresponding to the shape of the induction coil 6 . The furnace mouth magnetic shielding plate 9 is ring-shaped, and its aperture is compatible with the furnace mouth. The raw mater...
PUM
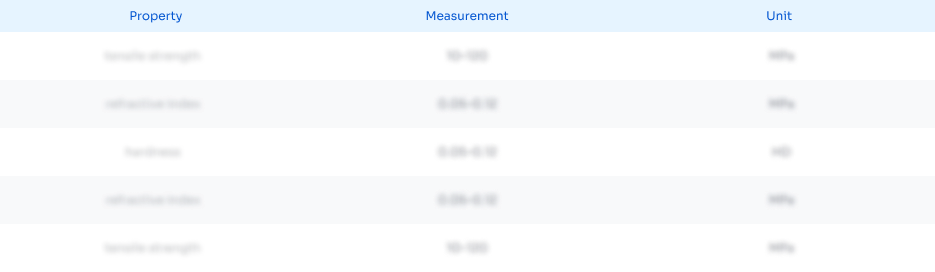
Abstract
Description
Claims
Application Information

- R&D Engineer
- R&D Manager
- IP Professional
- Industry Leading Data Capabilities
- Powerful AI technology
- Patent DNA Extraction
Browse by: Latest US Patents, China's latest patents, Technical Efficacy Thesaurus, Application Domain, Technology Topic, Popular Technical Reports.
© 2024 PatSnap. All rights reserved.Legal|Privacy policy|Modern Slavery Act Transparency Statement|Sitemap|About US| Contact US: help@patsnap.com