Model and control of a waste combustion process
A technology of combustion process and waste, applied in the direction of combustion type, controlled combustion, combustion method, etc., can solve the problems of increasing plant complexity, complex chemical process, unstable fuel quality, etc.
- Summary
- Abstract
- Description
- Claims
- Application Information
AI Technical Summary
Problems solved by technology
Method used
Image
Examples
Embodiment Construction
[0024] Figure 1 schematically shows a waste incineration plant with the following essential parts. An input feed mechanism or drive (10) directs municipal or industrial waste, garbage or other debris into the furnace (11) and rests the former on a supported movable grate (12), forming a waste bed. The grate (12) typically includes relatively movable grate plates for spreading, mixing and generally forward propelling of the waste on the grate (12). An auxiliary burner 13) may be provided to initiate or support the combustion process. The exhaust gases of the combustion are collected in the chimney and directed to the boiler (14) for heating the steam.
[0025] Without general loss, the incineration process is divided into four zones spanned in series by the waste: a drying zone (20), a first combustion zone (21) for pyrolysis and gasification / volatilization, for charred oxidation or solids Combustion residue zone (22) and ash handling / sintering zone (23). These zones are not...
PUM
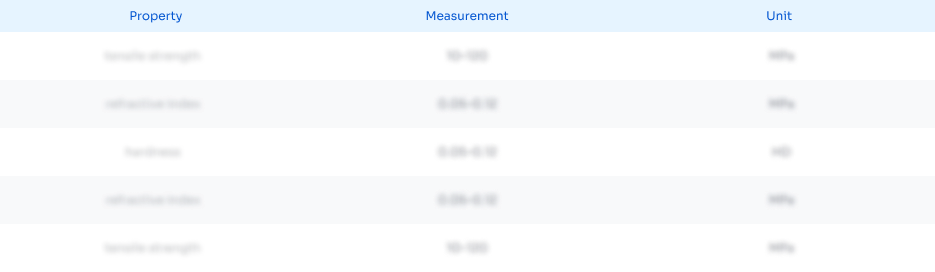
Abstract
Description
Claims
Application Information

- R&D
- Intellectual Property
- Life Sciences
- Materials
- Tech Scout
- Unparalleled Data Quality
- Higher Quality Content
- 60% Fewer Hallucinations
Browse by: Latest US Patents, China's latest patents, Technical Efficacy Thesaurus, Application Domain, Technology Topic, Popular Technical Reports.
© 2025 PatSnap. All rights reserved.Legal|Privacy policy|Modern Slavery Act Transparency Statement|Sitemap|About US| Contact US: help@patsnap.com