Precision polishing technique for stainless steel printed circuit board
A printed circuit board and precision polishing technology, applied in the field of electrolytic deburring treatment and precision polishing process, can solve the problems of high current density, long polishing time, affecting surface quality, etc., and achieve the effect of reasonable formula and simple and easy water treatment.
- Summary
- Abstract
- Description
- Claims
- Application Information
AI Technical Summary
Problems solved by technology
Method used
Examples
Embodiment 1
[0023] Use the stainless steel workpiece as the cathode, put NaOH and Na 2 CO 3 Perform electrolysis in the mixed solution to remove surface oil stains, and then wash with water. Then the stainless steel workpiece is used as the anode, and the lead plate is used as the cathode, and the stainless steel workpiece is put into the electrolytic solution for pretreatment electrolysis. At this time, the formula of the electrolytic solution is: (by weight), sulfuric acid 1.63%, phosphoric acid 0.58%, water 97.79% , the temperature is normal temperature, the current density is 5~10A / dm 2 , the time is 5-10 minutes, so that the large burrs remaining on the hole wall after laser cutting are removed, and the corrosion amount is within 0.001-0.002mm. After the pretreatment is completed, the stainless steel workpiece is used as the anode, and the lead plate is used as the cathode, and is electrolyzed for 1 minute in a precision electrolytic polishing solution. The formula of the electroly...
Embodiment 2
[0025] The difference between this embodiment 2 and embodiment 1 is that when the stainless steel workpiece is put into the electrolyte solution for pretreatment electrolysis in the present embodiment 2, the formula of the electrolyte solution used is: (by weight), sulfuric acid 1.64%, phosphoric acid 0.60%, water 97.76%, the temperature is normal temperature, the current density is 5~10A / dm 2 , time 5-10 minutes. After the pretreatment is completed, the stainless steel workpiece is also used as the anode, and the lead plate is used as the cathode, and is electrolyzed for 1 minute in the precision electrolytic polishing solution. The formula of the electrolyte used at this time is: (by weight), 27% sulfuric acid, 50% phosphoric acid , ammonium sulfate 0.04%, ammonium phosphate 0.01%, cellulose 0.03%, saccharin 0.006%, water 22.914%. Other processes and conditions are all the same.
PUM
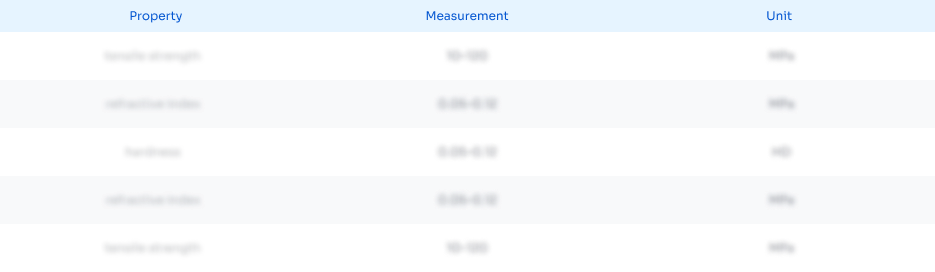
Abstract
Description
Claims
Application Information

- R&D
- Intellectual Property
- Life Sciences
- Materials
- Tech Scout
- Unparalleled Data Quality
- Higher Quality Content
- 60% Fewer Hallucinations
Browse by: Latest US Patents, China's latest patents, Technical Efficacy Thesaurus, Application Domain, Technology Topic, Popular Technical Reports.
© 2025 PatSnap. All rights reserved.Legal|Privacy policy|Modern Slavery Act Transparency Statement|Sitemap|About US| Contact US: help@patsnap.com