Catalytic cracking co-catalyst for high yield diesel oil and its preparing method
A co-catalyst, catalytic cracking technology, applied in catalytic cracking, cracking, petroleum industry and other directions, to achieve the effect of improving diesel yield, increasing utilization rate, and strong resistance to heavy metals
- Summary
- Abstract
- Description
- Claims
- Application Information
AI Technical Summary
Problems solved by technology
Method used
Examples
Embodiment 1
[0035] (1) Preparation of extraction product microspheres:
[0036] Add water to 1Kg (dry basis) kaolin from Suzhou, 0.1kg pseudoboehmite (calculated as alumina) and 8% water glass (calculated as silicon dioxide) to make a slurry, and spray to obtain 0.9Kg of spray microspheres. The sprayed microspheres were roasted in a muffle furnace at 920° C. for 3 hours to obtain roasted microspheres, which contained about 8% mullite. While stirring, 60 g of sodium hydroxide, 600 mL of deionized water, and 500 g of calcined microspheres were successively put into a stainless steel reactor, and the temperature was raised to 90° C. for 2 hours. After the reaction is completed, the mother liquor is removed by filtration, washed with hot deionized water until pH = 7, filtered and dried to obtain microspheres of the extraction product.
[0037] (2) post-treatment of extraction product to prepare co-catalyst:
[0038] Add 500ml of 1mol / l hydrochloric acid solution in a stainless steel kettle,...
Embodiment 2
[0042] (1) Preparation of extraction product microspheres:
[0043]2Kg (dry basis) kaolin produced in Suzhou, 0.4kg pseudoboehmite (calculated as alumina), 15% water glass and water were made into slurry, and 1.9Kg of spray microspheres were obtained in spray molding. The sprayed microspheres were roasted in a muffle furnace at 900°C for 2 hours to obtain roasted microspheres, which contained about 5% mullite. In a stirring state, 800 g of sodium hydroxide, 5 L of deionized water, and 1 kg of calcined microspheres were sequentially put into a stainless steel reactor, and the temperature was raised to 80° C. for 0.5 hours to react. After the reaction, the mother liquor was removed by filtration, washed with deionized water, and dried by filtration to obtain microspheres of the extraction product.
[0044] (2) post-treatment of extraction product to prepare co-catalyst:
[0045] Add 1l of 0.5mol / l hydrochloric acid solution in a stainless steel kettle, put in 200g of the extra...
Embodiment 3
[0049] (1) Preparation of extraction product microspheres:
[0050] 1.5Kg (dry basis) kaolin produced in Suzhou, 0.075kg pseudo-boehmite (calculated as alumina) and 12% water glass (calculated as silicon dioxide) are added with water to make a slurry, and spray molding obtains 1.2Kg of spray micro ball. The sprayed microspheres were roasted in a muffle furnace at 950° C. for 1 hour to obtain the roasted microspheres, which contained about 10% mullite. In a stirring state, 100 g of sodium hydroxide, 500 mL of deionized water, and 500 g of roasted microspheres were sequentially put into a stainless steel reactor, and the temperature was raised to 80° C. for 3.5 hours. After the reaction is finished, the mother liquor is removed by filtration, washed with hot deionized water until pH=7, filtered and dried to obtain microspheres of the extraction product.
[0051] (2) post-treatment of extraction product to prepare co-catalyst:
[0052] Add 100ml of 3mol / l hydrochloric acid sol...
PUM
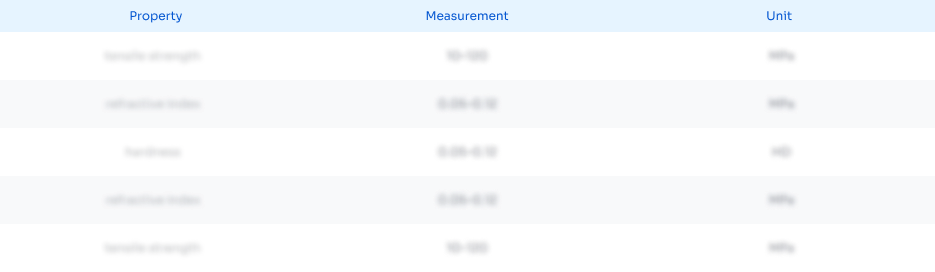
Abstract
Description
Claims
Application Information

- R&D
- Intellectual Property
- Life Sciences
- Materials
- Tech Scout
- Unparalleled Data Quality
- Higher Quality Content
- 60% Fewer Hallucinations
Browse by: Latest US Patents, China's latest patents, Technical Efficacy Thesaurus, Application Domain, Technology Topic, Popular Technical Reports.
© 2025 PatSnap. All rights reserved.Legal|Privacy policy|Modern Slavery Act Transparency Statement|Sitemap|About US| Contact US: help@patsnap.com