Modified kaolin
A kaolin, modified technology, applied in inorganic chemistry, catalyst carrier, non-metallic elements, etc., can solve the problems of difficult filtration, difficult to large-scale industrial production, etc., to achieve the effect of improving performance and strong resistance to heavy metals
- Summary
- Abstract
- Description
- Claims
- Application Information
AI Technical Summary
Problems solved by technology
Method used
Examples
Embodiment 1
[0019] Embodiment 1 A kind of modified kaolin is prepared by the following steps:
[0020] S1, mixed material: kaolin with crystalline kaolinite content ≥ 95% is roasted at 800-1200°C for 5-8 hours, and then cooled to obtain roasted kaolin. The roasted kaolin, aluminum source (metal aluminum powder), and zinc source are added (Metal zinc powder) and acid (mixed acid with a concentration of 3M) were added to the container, and stirred evenly to obtain a mixed material with a solid content of 15%; the mixed material was treated with ultrasonic oscillation at a frequency of 30-40kHz for 25 minutes;
[0021] Wherein, the consumption of acid is that the surface of the calcined kaolin, the added aluminum source, and the added zinc source are covered; the mixed acid is prepared by perchloric acid and sulfuric acid according to a volume ratio of 1.5:3;
[0022] S2, filtering the mixed material prepared in step S1, washing the product with deionized water to obtain a mixed slurry;
[...
Embodiment 2
[0024] Embodiment 2 A modified kaolin is prepared by the following steps:
[0025] S1, mixed material: kaolin with crystalline kaolinite content ≥ 95% is roasted at 800-1200°C for 5-8 hours, and then cooled to obtain roasted kaolin. The roasted kaolin, aluminum source (metal aluminum powder), and zinc source are added (Metal zinc powder) and acid (mixed acid with a concentration of 1M) were added to the container, and stirred evenly to obtain a mixed material with a solid content of 10%; the mixed material was treated with ultrasonic oscillation at a frequency of 30-40kHz for 20 minutes;
[0026] Wherein, the dosage of the acid is to cover the surface of the calcined kaolin, the added aluminum source, and the added zinc source; the mixed acid is prepared by nitric acid and sulfuric acid according to a volume ratio of 1:3;
[0027] S2, filtering the mixed material prepared in step S1, washing the product with deionized water to obtain a mixed slurry;
[0028] S3, putting the m...
Embodiment 3
[0029] Embodiment 3 A kind of modified kaolin is prepared by the following steps:
[0030] S1, mixed material: kaolin with crystalline kaolinite content ≥ 95% is roasted at 800-1200°C for 5-8 hours, and then cooled to obtain roasted kaolin. The roasted kaolin, aluminum source (metal aluminum powder), and zinc source are added (Metal zinc powder) and acid (mixed acid with a concentration of 5M) were added to the container, and stirred evenly to obtain a mixed material with a solid content of 20%; the mixed material was treated with ultrasonic oscillation at a frequency of 30-40kHz for 30 minutes;
[0031] Wherein, the amount of acid is to cover the surface of the roasted kaolin, the added aluminum source, and the added zinc source; the mixed acid is prepared by hydrochloric acid and sulfuric acid at a volume ratio of 1:3;
[0032] S2, filtering the mixed material prepared in step S1, washing the product with deionized water to obtain a mixed slurry;
[0033] S3, putting the mi...
PUM
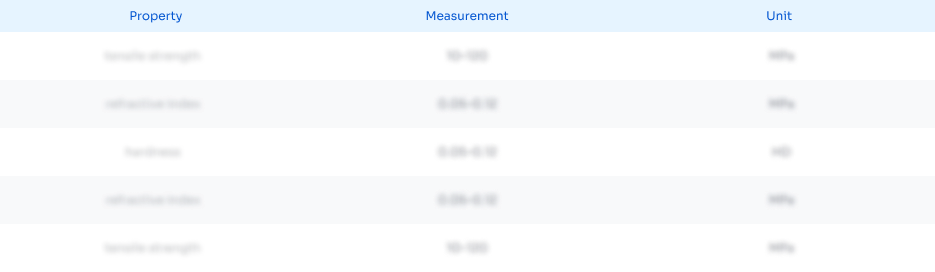
Abstract
Description
Claims
Application Information

- R&D
- Intellectual Property
- Life Sciences
- Materials
- Tech Scout
- Unparalleled Data Quality
- Higher Quality Content
- 60% Fewer Hallucinations
Browse by: Latest US Patents, China's latest patents, Technical Efficacy Thesaurus, Application Domain, Technology Topic, Popular Technical Reports.
© 2025 PatSnap. All rights reserved.Legal|Privacy policy|Modern Slavery Act Transparency Statement|Sitemap|About US| Contact US: help@patsnap.com