Process for preparing epoxy chloropropane
A technology of epichlorohydrin and chloropropene, applied in the direction of organic chemistry, can solve the problems of large calcium chloride-containing wastewater, environmental pollution, and unindustrialization
- Summary
- Abstract
- Description
- Claims
- Application Information
AI Technical Summary
Problems solved by technology
Method used
Image
Examples
example 1
[0029] Example 1. Epoxidation of allyl chloride:
[0030] Get 0.23g catalyzer (the total package is composed of {π-C 5 h 5 N + C 12 h 25} 3 {PMo 4 o 16} 3- ), 3.30gH 2 o 2 Solution (33.5wt%) was added with 10 g of allyl chloride, and reacted at 65° C. for 2 hours. Allyl chloride to H 2 o 2 The conversion rate was 92.7%, the epichlorohydrin selectivity was 92.2%, and the yield was 85.5%. The catalyst recovery rate was 99.8%.
example 2
[0031] Example 2. Epoxidation of allyl chloride
[0032] Take 0.38g catalyst {C 16 h 33 N + (CH 3 ) 3} 3 {PO 4 [WO(O 2 ) 2 ] 2 [WO(O 2 ) 2 (H 2 O)]} 3- , 0.02g potassium hydrogen phthalate, 2.50gH 2 o 2 solution (35.0wt%), add 10g of allyl chloride, and react at 65° C. for 2.5 hours. Allyl chloride to H 2 o 2 The conversion rate was 95%, the epichlorohydrin selectivity was 90%, and the yield was 85.5%. Centrifuge to recover the catalyst. After washing with toluene, dry it. Gained reclaimed catalyst can be recycled, and its reaction result is as table 1:
[0033] catalyst cycle
example 3
[0034] Example 3. Epoxidation of allyl chloride
[0035] Get 0.29g catalyzer (the total package is composed of {π-C 5 h 5 N + C 14 h 29} 3 {PW 3.75 h 0.5 o 15.5} 3- ), add 0.02gNaH 2 PO 4 / 0.02gNa 2 HPO 4 Mixed Phosphates, 1.65gH 2 o 2 Solution (33.5wt%) was added with 10 g of allyl chloride, and reacted at 45° C. for 3 hours. Allyl chloride to H 2 o 2 The conversion rate was 93.3%, the epichlorohydrin selectivity was 95.1%, and the yield was 88.7%. Centrifuge to recover the catalyst. After washing with allyl chloride, dry it. Gained recovery catalyst can be recycled, and its activity is shown in Table 2:
[0036] catalyst cycle
PUM
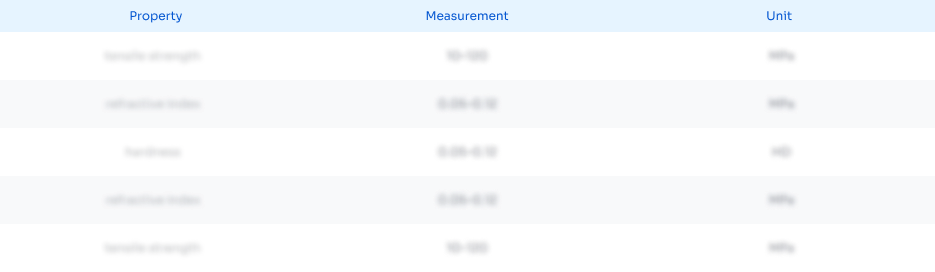
Abstract
Description
Claims
Application Information

- R&D Engineer
- R&D Manager
- IP Professional
- Industry Leading Data Capabilities
- Powerful AI technology
- Patent DNA Extraction
Browse by: Latest US Patents, China's latest patents, Technical Efficacy Thesaurus, Application Domain, Technology Topic, Popular Technical Reports.
© 2024 PatSnap. All rights reserved.Legal|Privacy policy|Modern Slavery Act Transparency Statement|Sitemap|About US| Contact US: help@patsnap.com