Lithium-iron disulfide anode materials and method for preparing same
A technology of iron disulfide battery and positive electrode material, which is applied to the electrodes, battery electrodes, circuits and other directions of primary batteries, and can solve problems such as no technical solutions for modification treatment of natural iron disulfide materials.
- Summary
- Abstract
- Description
- Claims
- Application Information
AI Technical Summary
Problems solved by technology
Method used
Examples
Embodiment 1
[0026] Embodiment one. Take by weighing natural iron disulfide fine powder 25g. Add 10 g of absolute ethanol and ball mill for 5 hours in a ball mill jar full of nitrogen. The ball-milled iron disulfide material was baked in a vacuum oven at 120° C. for 6 hours. Weigh 0.5g of conductive graphite and mix evenly with ball-milled iron disulfide material, disperse in a beaker with 50ml of deionized water, and add 1mol / l TiCl 4 Solution 12ml. Then, under magnetic stirring, add 12ml of 4mol / l ammonia solution to make it mix with TiCl 4 The solution carries out metathesis reaction (when using other metal salt solutions, the addition amount of alkali solution is also determined according to the theoretical stoichiometric ratio of carrying out metathesis reaction with the metal salt used). After reacting for 1 hour under stirring, filter the product, wash it several times with deionized water, bake it in a common oven at 60°C for 10 hours, and finally bake it at 400°C for 15 hours i...
Embodiment 2
[0027] Embodiment two. Take by weighing natural iron disulfide fine powder 25g. Add 25g of acetone and ball mill for 30 hours in a ball mill jar full of nitrogen. The iron disulfide material after ball milling was baked in a vacuum oven at 60°C for 24 hours. Weigh 1g of acetylene black and mix it evenly with ball-milled iron disulfide material, disperse it in a beaker filled with 80ml deionized water, and add 1mol / l MgCl 2 Solution 18ml. Then, under magnetic stirring, add 18ml of 2mol / l ammonia solution to make it mix with MgCl 2 The solution undergoes a metathesis reaction. After reacting under stirring for 30 minutes, filter the product, wash it several times with deionized water, and bake it in a common oven at 120°C for 2 hours, and finally bake it at 200°C for 24 hours in a nitrogen atmosphere to obtain the coating described in this patent. Conductivity of MgO and good voltage platform of FeS 2 Composite cathode material. The material was used for battery testing, a...
Embodiment 3
[0028] Embodiment three. Take by weighing natural iron disulfide fine powder 25g. Add 15g of cyclohexanone and ball mill for 15 hours in a ball mill jar full of nitrogen. The iron disulfide material after ball milling was baked for 2 hours under vacuum at 200°C. Take by weighing the mixture of 2.5g conductive graphite and acetylene black (conductive graphite: acetylene black=2: 1) the ferric disulfide material after ball milling is evenly mixed, is dispersed in the beaker that 150ml deionized water is housed, and adds 1mol / l AlPO 4 Solution 6ml, then, under magnetic stirring, add 3mol / l ammonia solution 6ml, make it mix with AlPO 4 The solution undergoes a metathesis reaction. After reacting for 1 hour under stirring, filter the product, wash it several times with deionized water, bake it in a common oven at 80°C for 6 hours, and finally bake it at 600°C for 10 hours in a nitrogen atmosphere to obtain the package described in this patent. Cover Al 2 o 3 FeS with good con...
PUM
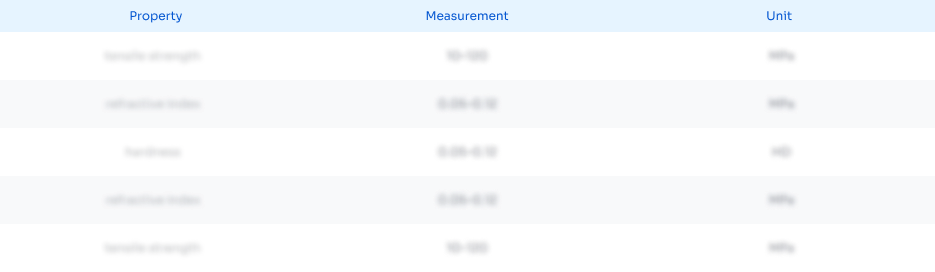
Abstract
Description
Claims
Application Information

- Generate Ideas
- Intellectual Property
- Life Sciences
- Materials
- Tech Scout
- Unparalleled Data Quality
- Higher Quality Content
- 60% Fewer Hallucinations
Browse by: Latest US Patents, China's latest patents, Technical Efficacy Thesaurus, Application Domain, Technology Topic, Popular Technical Reports.
© 2025 PatSnap. All rights reserved.Legal|Privacy policy|Modern Slavery Act Transparency Statement|Sitemap|About US| Contact US: help@patsnap.com