Process of continuously leaching manganese oxide ore
A technology for leaching manganese oxide ore, which is applied in the field of continuous leaching of manganese oxide ore with good continuity, can solve the problems of long turnaround time, increase in the number of equipment used, and reduce the effective utilization rate of equipment, so as to achieve good continuity, reduce labor intensity, The effect of reducing the number of
- Summary
- Abstract
- Description
- Claims
- Application Information
AI Technical Summary
Problems solved by technology
Method used
Examples
Embodiment 1
[0009] Manganese oxide ore powder containing 19.14% manganese, pyrite powder with sulfur content of 44.54%, and sulfuric acid with a concentration of 98% are used to prepare a 100g / l dilute sulfuric acid solution. Manganese oxide ore powder, pyrite The acid-mineral ratio of powder and sulfuric acid is 1:0.21:0.46. Shuangfei powder is used as the neutralizing agent. The continuous leaching tank used is composed of three leaching tanks connected in series to form a three-stage continuous leaching. The effective volume of each leaching tank is 1m 3 / piece, one neutralization tank, the effective volume is 1.5m 3 To realize the method of the present invention.
[0010] Mix the above-mentioned manganese oxide ore powder and pyrite powder in a dry weight ratio of 1:0.21, and then continuously add them to the first-stage leaching tank of the continuous leaching tank at the same time with the prepared sulfuric acid in a ratio of 1:0.46, and continuously Stir, the material liquid ove...
Embodiment 2
[0012] Manganese oxide powder containing 20.06% manganese, pyrite powder with sulfur content of 42.37%, and sulfuric acid with a concentration of 98% are used to prepare a 90g / l dilute sulfuric acid solution. Manganese oxide powder, pyrite The acid-mineral ratio of powder and sulfuric acid is 1:0.22:0.45. Ammonia water is used as the neutralizing agent. The continuous leaching tank used is composed of four leaching tanks connected in series to form four-stage continuous leaching. The effective volume of each leaching tank is 1m 3 / piece, one neutralization tank, the effective volume is 1.5m 3 To realize the method of the present invention.
[0013] Mix the above-mentioned manganese oxide ore powder and pyrite powder in a dry weight ratio of 1:0.22 to form a mixture of two ores and a manganese sulfate solution with a free sulfuric acid concentration of 90g / l in a ratio of 1:0.45 and continuously add them to the continuous leaching tank In the first-stage leaching tank, while ...
PUM
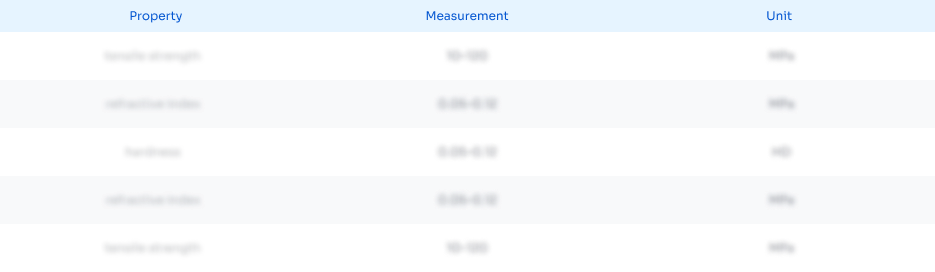
Abstract
Description
Claims
Application Information

- R&D Engineer
- R&D Manager
- IP Professional
- Industry Leading Data Capabilities
- Powerful AI technology
- Patent DNA Extraction
Browse by: Latest US Patents, China's latest patents, Technical Efficacy Thesaurus, Application Domain, Technology Topic, Popular Technical Reports.
© 2024 PatSnap. All rights reserved.Legal|Privacy policy|Modern Slavery Act Transparency Statement|Sitemap|About US| Contact US: help@patsnap.com