Guar gum natural silk printing paste and method for preparing same
A technology of printing paste and guar gum, which is applied in dyeing, textiles and papermaking, etc., to achieve good block surface uniformity, improve physical and chemical properties, and reduce energy consumption
- Summary
- Abstract
- Description
- Claims
- Application Information
AI Technical Summary
Problems solved by technology
Method used
Image
Examples
Embodiment 1
[0059] Embodiment 1: A kind of guar gum silk printing paste and preparation method thereof
[0060] see figure 1 As shown, add 550g methanol and 250g guar gum in a 1000ml three-necked flask, stir for 10min and add 52g of 30% liquid caustic soda (sodium hydroxide), 10g of 80% triethanolamine, 10g of 5% acetone, 12g of 37.5% formaldehyde and 27.5% H 2 o 2 54g, the temperature was raised to 50°C for 2h, and the reaction was carried out. Then, add 30% liquid caustic soda 52g, in reaction vessel, pass nitrogen 5 minutes, rush into oxirane (gas) under nitrogen protection state, control speed (about 30g), the time is 2 hours. Then, cool to 40°C, neutralize to pH=6.5 with hydrochloric acid, and filter. The filter cake was washed with methanol for 50 min and filtered. Dry the filter cake, grind it finely, pass through a 200-mesh sieve, and blend the preservative (phenol or paraben) and complexing agent (sodium hexametaphosphate) to obtain 290 g of the finished product.
Embodiment 2
[0061] Embodiment 2: a kind of guar gum silk printing paste and preparation method thereof
[0062] see figure 1 As shown, add 550g methanol and 250g guar gum in a 1000ml three-necked flask, stir for 10min and add 40g of 30% liquid caustic soda (sodium hydroxide), 10g of 80% triethanolamine, 10g of 5% acetone, 12g of 37.5% formaldehyde and 27.5% H 2 o 2 52g, the temperature was raised to 48°C for 2h, and the reaction was carried out. Then, add 50g of 30% liquid caustic soda, feed nitrogen into the reaction vessel for 5 minutes, rush into ethylene oxide under nitrogen protection state, control the speed (about 40g), and the time is 2 hours. Then, cool to 40°C, neutralize with hydrochloric acid to pH=6.5, and filter. Wash the filter cake with methanol for 50 minutes and filter, dry the filter cake, grind it finely, pass it through a 200-mesh sieve, and mix the preservative (phenol or paraben) and complexing agent (sodium hexametaphosphate) to obtain 300 g of the finished prod...
Embodiment 3
[0063] Embodiment 3: a kind of guar gum silk printing paste and preparation method thereof
[0064] see figure 1 As shown, add 550g methanol and 250g guar gum to a 1000ml three-necked flask, stir for 10min and add 58g of 30% liquid caustic soda, 10g of 80% triethanolamine, 10g of 5% acetone, 12g of 37.5% formaldehyde and 27.5% H 2 o 2 56g, the temperature was raised to 52°C for 2h, and the reaction was carried out. Then, add 54g of 30% liquid caustic soda, feed nitrogen into the reaction vessel for 5 minutes, pour ethylene oxide under nitrogen protection state, control the speed (about 60g), and carry out the etherification reaction for 2 hours. Then, cool to 40°C, neutralize with hydrochloric acid to pH=6.5, and filter. Wash the filter cake with methanol for 50 minutes and filter, dry the filter cake, grind it finely, pass it through a 200-mesh sieve, and blend preservative (phenol or paraben) and complexing agent (sodium hexametaphosphate) to obtain 310 g of finished prod...
PUM
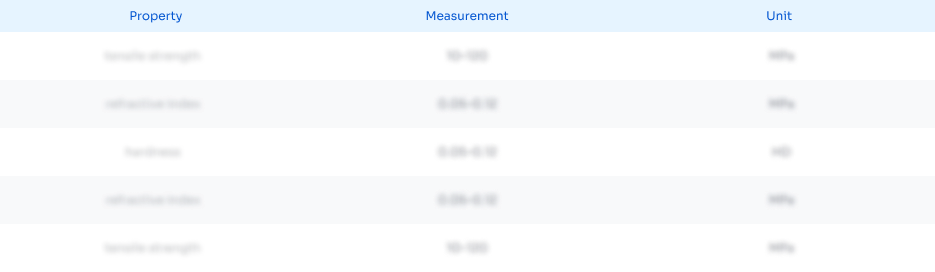
Abstract
Description
Claims
Application Information

- R&D
- Intellectual Property
- Life Sciences
- Materials
- Tech Scout
- Unparalleled Data Quality
- Higher Quality Content
- 60% Fewer Hallucinations
Browse by: Latest US Patents, China's latest patents, Technical Efficacy Thesaurus, Application Domain, Technology Topic, Popular Technical Reports.
© 2025 PatSnap. All rights reserved.Legal|Privacy policy|Modern Slavery Act Transparency Statement|Sitemap|About US| Contact US: help@patsnap.com