Compound titanium silicon molecular sieve with middle and micro pore, its preparation and use
A silicon molecular sieve and composite titanium technology, which is applied in molecular sieve catalysts, refined hydrocarbon oil, chemical instruments and methods, etc., can solve the problems of long crystallization and harsh synthesis conditions, and achieve mild synthesis conditions, stability and catalytic oxidation ability. , the effect of good catalytic oxidation performance
- Summary
- Abstract
- Description
- Claims
- Application Information
AI Technical Summary
Problems solved by technology
Method used
Examples
Embodiment 1
[0029]Add 11.2ml of tetraethylsilicate to 25.6ml of tetrapropylammonium hydroxide solution, stir at room temperature for 1-2 hours; take 0.4ml of tetrabutyl titanate and dissolve in 4ml of isopropanol, mix well and slowly drop into the above solution, subject to no precipitation; then add 4.3ml of deionized water and continue stirring for 0.5-1.5h. The mixture was warmed up to 80 °C, stirred and heated for 1 h, and 15 ml of deionized water was added. The resulting mixture was transferred into a stainless steel crystallization kettle with a polytetrafluoroethylene liner, statically crystallized at 140 °C for 2.5 h, and rapidly cooled to room temperature to obtain a precursor containing TS-1 nanoparticles. Dissolve 2.5g of dodecylamine in 10ml of absolute ethanol, add 15ml of deionized water, stir and mix evenly, drop the precursor obtained above into the mixture, and keep stirring at room temperature for 24h. The product was filtered, washed, dried, and calcined at 640°C for 4...
Embodiment 2
[0031] Add 11.2ml of tetraethylsilicate to 25.6ml of tetrapropylammonium hydroxide solution, stir at room temperature for 1-2 hours; take 0.4ml of tetrabutyl titanate and dissolve in 4ml of isopropanol, mix well and slowly drop into the above solution, subject to no precipitation; then add 4.3ml of deionized water and continue stirring for 0.5-1.5h. The mixture was warmed up to 80 °C, stirred and heated for 1 h, and 15 ml of deionized water was added. The resulting mixture was transferred into a stainless steel crystallization kettle lined with polytetrafluoroethylene, statically crystallized at 100 °C for 6 h, and rapidly cooled to room temperature to obtain a precursor containing TS-1 nanoparticles. Take 2.5g of dodecylamine and dissolve it in 10ml of absolute ethanol, add 15ml of deionized water, stir and mix evenly, drop the precursor obtained above into the mixture, and keep stirring at room temperature for 9h. The product was filtered, washed, dried, and calcined at 640...
Embodiment 3
[0033] Add 11.2ml of tetraethylsilicate to 25.6ml of tetrapropylammonium hydroxide solution, stir at room temperature for 1-2 hours; take 0.4ml of tetrabutyl titanate and dissolve in 4ml of isopropanol, mix well and slowly drop into the above solution, subject to no precipitation; then add 4.3ml of deionized water and continue stirring for 0.5-1.5h. The mixture was warmed up to 80 °C, stirred and heated for 1 h, and 15 ml of deionized water was added. The obtained mixture was transferred into a stainless steel crystallization kettle lined with polytetrafluoroethylene, statically crystallized at 60°C for 48h, and rapidly cooled to room temperature to obtain a precursor containing TS-1 nanoparticles. Take 2.5g of dodecylamine and dissolve it in 10ml of absolute ethanol, add 15ml of deionized water, stir and mix evenly, drop the precursor obtained above into the mixture, and keep stirring at room temperature for 18h. The product was filtered, washed, dried, and calcined at 640°C...
PUM
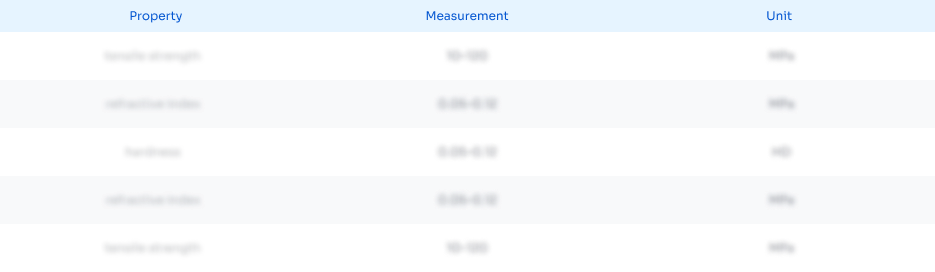
Abstract
Description
Claims
Application Information

- R&D
- Intellectual Property
- Life Sciences
- Materials
- Tech Scout
- Unparalleled Data Quality
- Higher Quality Content
- 60% Fewer Hallucinations
Browse by: Latest US Patents, China's latest patents, Technical Efficacy Thesaurus, Application Domain, Technology Topic, Popular Technical Reports.
© 2025 PatSnap. All rights reserved.Legal|Privacy policy|Modern Slavery Act Transparency Statement|Sitemap|About US| Contact US: help@patsnap.com