Method and device for friction stir welding
A friction stirring and joining method technology, applied in welding equipment, metal processing equipment, manufacturing tools, etc., can solve the problems of tool length elongation, needle thermal expansion, small spacing, etc., to ensure the effect of joint strength
- Summary
- Abstract
- Description
- Claims
- Application Information
AI Technical Summary
Problems solved by technology
Method used
Image
Examples
Embodiment Construction
[0039] will be combined below Figure 1-5 An example of the present invention will be described. Such as figure 1 As shown, the friction stir welding apparatus 1 cools the upper tool 2 and the lower tool 3 by the air injected from the respective air nozzles 4, 5, and resists the friction caused by the rotating upper tool 2 and the workpiece 6 (parts to be joined 6a, 6b). The thermal expansion of each tool 2, 3 caused by heat is suppressed. Therefore, this friction stir welding device 1 is configured to properly maintain the gap G between the upper tool 2 and the lower tool 3 during friction stir welding, as image 3 As shown, forming the friction stir welded portion 7 having an appropriate thickness of the remaining mother plate thickness T between the overlapped workpieces 6 ensures the joint strength of the friction stir welded portion 7 . Furthermore, as shown in FIG. 2 , the friction stir welding device 1 is equipped with a non-contact temperature sensor 8 (tool tempera...
PUM
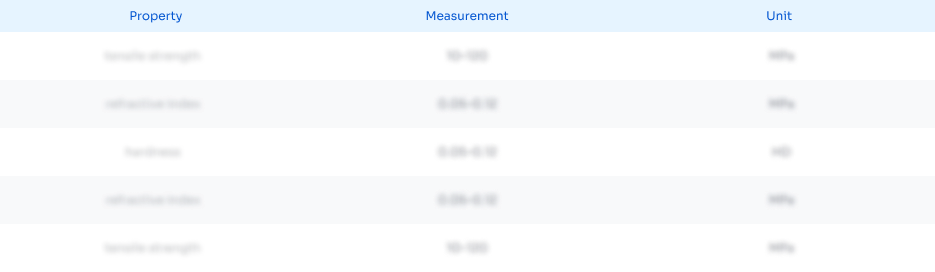
Abstract
Description
Claims
Application Information

- R&D
- Intellectual Property
- Life Sciences
- Materials
- Tech Scout
- Unparalleled Data Quality
- Higher Quality Content
- 60% Fewer Hallucinations
Browse by: Latest US Patents, China's latest patents, Technical Efficacy Thesaurus, Application Domain, Technology Topic, Popular Technical Reports.
© 2025 PatSnap. All rights reserved.Legal|Privacy policy|Modern Slavery Act Transparency Statement|Sitemap|About US| Contact US: help@patsnap.com