Preparation of original bamboo fiber by bioenzyme method
A bamboo raw fiber and bio-enzyme technology, applied in the field of making bamboo raw fiber for textile and natural bamboo fiber for textile, can solve the problems of unstable quality, environmental pollution, long cycle, etc., and achieve product quality Stability, high purity, and short processing time
- Summary
- Abstract
- Description
- Claims
- Application Information
AI Technical Summary
Problems solved by technology
Method used
Examples
Embodiment 1
[0014] A kind of bio-enzyme method produces the raw bamboo fiber for weaving, and its production process is:
[0015] 1. Cut off the moso bamboo and cut it into bamboo slices, boil it in boiling water for 1 hour, take it out, crush it, and hammer it into filaments. Then put it in a pressure cooker and cook at 120°C for 4 hours to remove part of pectin, hemicellulose and lignin;
[0016] 2. The above-mentioned pretreated bamboo shreds were immersed in a solution of 1.0 mg / ml pectinase, 1.0 mg / ml hemicellulase, and 2.0 mg / ml ligninase at 40 ° C for 7 days;
[0017] 3. Take out the bamboo cellulose fibers decomposed by enzymes, wash them, bleach them, oil them, soften them, and loosen them to obtain bamboo fibers with an average fineness of 1050 metric pieces.
Embodiment 2
[0019] A kind of bio-enzyme method produces the raw bamboo fiber for weaving, and its production process is:
[0020] 1. Cut off the green bamboo skin and cut it into bamboo slices, put it in boiling water and boil for 2 hours, take it out, crush it, and hammer it into filaments. Then put it in a pressure cooker and cook at 100°C for 6 hours to remove part of pectin, hemicellulose and lignin;
[0021] 2. Immerse the above-mentioned pretreated bamboo shreds in a solution of 20 mg / ml pectinase, 15 mg / ml hemicellulase, 20 mg / ml ligninase and 5 mg / ml cellulase at 30 °C 3 days for processing;
[0022] 3. Take out the bamboo cellulose fibers decomposed by enzymes, wash them, bleach them, oil them, soften them, and loosen them to obtain raw bamboo fibers with an average fineness of 2,700 metric pieces.
Embodiment 3
[0024] A kind of bio-enzyme method produces the raw bamboo fiber for weaving, and its production process is:
[0025] 1. Cut off the moso bamboo and cut it into small pieces, boil it in boiling water for 1.5 hours, take it out, crush it, and hammer it into filaments. Then put it in a pressure cooker and cook at 110°C for 3 hours to remove part of the pectin, hemicellulose and lignin;
[0026] 2. The above-mentioned pretreated bamboo shreds were immersed in a solution of 50 mg / ml pectinase, 40 mg / ml hemicellulase and 50 mg / ml ligninase at 60 ° C for 4 days;
[0027] 3. Take out the bamboo cellulose fibers decomposed by enzymes, wash them, bleach them, oil them, soften them, and loosen them to obtain raw bamboo fibers with an average fineness of 2650 metric pieces.
PUM
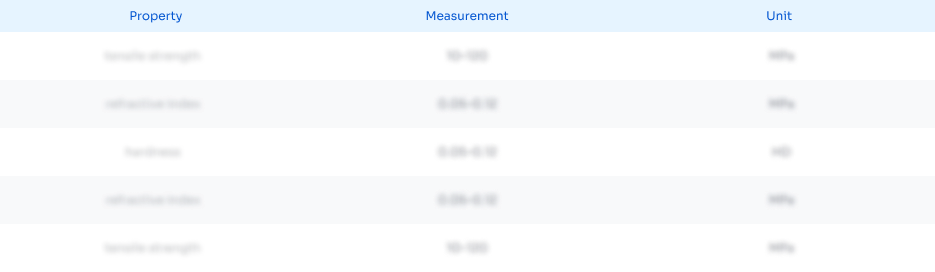
Abstract
Description
Claims
Application Information

- R&D Engineer
- R&D Manager
- IP Professional
- Industry Leading Data Capabilities
- Powerful AI technology
- Patent DNA Extraction
Browse by: Latest US Patents, China's latest patents, Technical Efficacy Thesaurus, Application Domain, Technology Topic, Popular Technical Reports.
© 2024 PatSnap. All rights reserved.Legal|Privacy policy|Modern Slavery Act Transparency Statement|Sitemap|About US| Contact US: help@patsnap.com