Composite material product of permanent magnetic ferrite material and ceramic material and its producing process
A technology of permanent magnet ferrite and ceramic materials, which is applied in the field of magnetic materials and ceramics, can solve the problems that the scope of use and the effect of use have not been brought into full play, and the processing efficiency of permanent magnet ferrite is poor, so as to achieve a reasonable design of the production process , strong wear resistance, stable and reliable process
- Summary
- Abstract
- Description
- Claims
- Application Information
AI Technical Summary
Problems solved by technology
Method used
Examples
Embodiment 1
[0015] 1. In the production process of ferrite devices, 94 kg of ferric oxide, the raw material of permanent magnet ferrite, is used as the main raw material, mixed with 6 kg of polyvinyl alcohol as the binder, and the weight percentage of ferric oxide and polyvinyl alcohol is mixed It is 94% of ferric oxide and 6% of polyvinyl alcohol. The magnetic material blank is pressed on the hydraulic press through the mold, and then sintered at 1100°C for 12 hours, and then cooled with the furnace for 12 hours to make a semi-finished product; Fine grinding is made into permanent magnet ferrite devices.
[0016] 2. The surface of the finished permanent magnet ferrite is coated with ceramic material, and sintered at a high temperature of 1000°C to permanently bond the ceramic material on the surface of the device.
[0017] 3. Coat the surface of the ceramic layer of the permanent magnet ferrite device with blue and white materials and pastel materials, burn them at a temperature of 700°C...
Embodiment 2
[0020] 1. In the production process of ferrite devices, 96 kg of ferric oxide, the raw material of permanent magnet ferrite, is used as the main raw material, mixed evenly with 4 kg of adhesive polyvinyl alcohol, and the mixed weight percentage of ferric oxide and polyvinyl alcohol is It is 96% of ferric oxide and 4% of polyvinyl alcohol. Press the magnetic material blank on the hydraulic press through the mold, then sinter at 1115°C for 13 hours, and then cool down with the furnace for 11 hours to make a semi-finished product; Fine grinding is made into permanent magnet ferrite devices.
[0021] 2. The finished surface of the finished permanent magnet ferrite is coated with ceramic material, and then sintered at a high temperature of 1050°C to permanently bond the ceramic material on the surface of the device.
[0022] 3. Coat the surface of the ceramic layer of the permanent magnet ferrite device with blue and white materials and pastel materials, burn them at 800°C for 16 h...
Embodiment 3
[0025] 1. In the production process of ferrite devices, 98 kg of ferric oxide, the raw material of permanent magnet ferrite, is used as the main raw material, mixed evenly with 2 kg of adhesive polyvinyl alcohol, and the mixed weight percentage of ferric oxide and polyvinyl alcohol is It is 98% of ferric oxide and 2% of polyvinyl alcohol. The magnetic material blank is pressed on the hydraulic press through the mold, and then sintered at 1200°C for 14 hours, and then cooled with the furnace for 10 hours to make a semi-finished product; Fine grinding is made into permanent magnet ferrite devices.
[0026] 2. The finished surface of the finished permanent magnet ferrite is coated with ceramic material, and sintered at a high temperature of 1100°C to permanently bond the ceramic material on the surface of the device.
[0027] 3. Coat the surface of the ceramic layer of the permanent magnet ferrite device with blue and white materials and pastel materials, burn them at 900°C for 1...
PUM
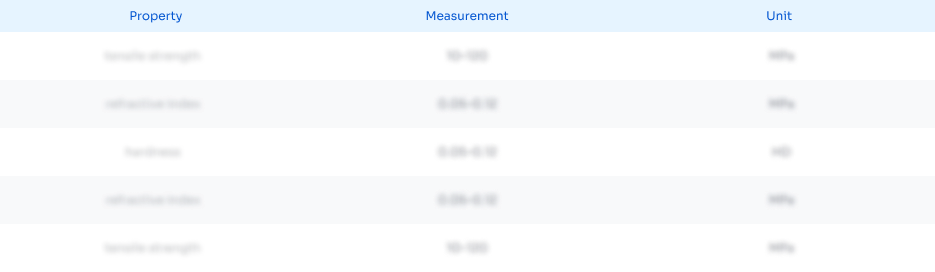
Abstract
Description
Claims
Application Information

- Generate Ideas
- Intellectual Property
- Life Sciences
- Materials
- Tech Scout
- Unparalleled Data Quality
- Higher Quality Content
- 60% Fewer Hallucinations
Browse by: Latest US Patents, China's latest patents, Technical Efficacy Thesaurus, Application Domain, Technology Topic, Popular Technical Reports.
© 2025 PatSnap. All rights reserved.Legal|Privacy policy|Modern Slavery Act Transparency Statement|Sitemap|About US| Contact US: help@patsnap.com