Method for manufacturing substrate with emergent points
A manufacturing method and protruding point technology are applied in the field of manufacturing substrates with protruding points, which can solve problems such as difficult protruding points, inability to select the height of protruding points 108, and inability to install circuit components at the same time, and achieve reliable electrical connection and manufacturing process. The effect of simplifying and improving accuracy
- Summary
- Abstract
- Description
- Claims
- Application Information
AI Technical Summary
Problems solved by technology
Method used
Image
Examples
Embodiment Construction
[0048] refer to Figure 1 ~ Figure 3 The method of manufacturing the circuit board of this embodiment will be described.
[0049] First, refer to figure 1 (A), the substrate 11 with the first conductive foil 12 pasted on the top and the second conductive foil 13 pasted on the bottom is prepared.
[0050] As the substrate 11, a glass epoxy substrate or a glass polyimide substrate is preferably used, but a fluorine substrate, a glass PPO substrate, a ceramic substrate, etc. may also be used depending on circumstances. In addition, flexible boards, films, and the like can also be used. In this embodiment, a glass epoxy substrate having a thickness of approximately 200 μm is used.
[0051] As the first conductive foil 12 and the second conductive foil 13, any metal that can be etched may be used. In this form, metal foil made of copper is used. Furthermore, copper foil having a film thickness of about 175 μm is used for the first conductive foil 12 . This film thickness is ...
PUM
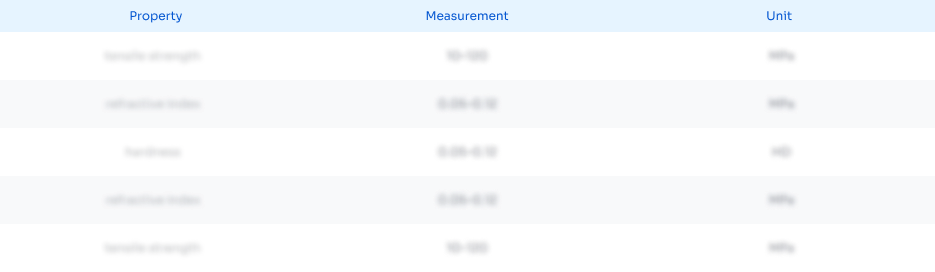
Abstract
Description
Claims
Application Information

- R&D
- Intellectual Property
- Life Sciences
- Materials
- Tech Scout
- Unparalleled Data Quality
- Higher Quality Content
- 60% Fewer Hallucinations
Browse by: Latest US Patents, China's latest patents, Technical Efficacy Thesaurus, Application Domain, Technology Topic, Popular Technical Reports.
© 2025 PatSnap. All rights reserved.Legal|Privacy policy|Modern Slavery Act Transparency Statement|Sitemap|About US| Contact US: help@patsnap.com