Treatment method of dehydration in ethylene glycol production
A technology of ethylene glycol and dehydration tower, applied in the field of dehydration treatment in ethylene glycol production, can solve the problem of easy coking of reboilers, and achieve the effects of slow coking speed, significant economic benefits and good economic effects
- Summary
- Abstract
- Description
- Claims
- Application Information
AI Technical Summary
Problems solved by technology
Method used
Image
Examples
Embodiment Construction
[0038] Below to figure 2 The schemes shown are examples to further describe the method of the invention. The scope of the present invention is not limited by the examples, and the scope of the present invention is set forth in the claims.
[0039] Such as figure 2 As shown, a preheater is added to the feed pipeline of the dehydration tower of the existing production device, and a tube and tube heat exchanger is used for heating with medium-pressure steam of about 1.0MpaG (gauge pressure). The number of trays in the dehydration tower is 30, the temperature at the top of the tower is 60-65°C, the temperature at the bottom of the tower is 160-170°C, and the pressure inside the tower is 20-40kPa.
[0040] The concentrated ethylene glycol aqueous solution obtained from the final effect evaporator is introduced into the preheater and heated to its bubble point temperature, 140°C; then the ethylene glycol aqueous solution is introduced from the 16th to 18th plates of the dehydrat...
PUM
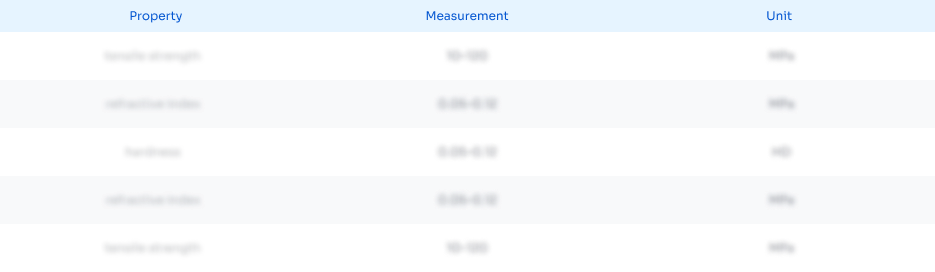
Abstract
Description
Claims
Application Information

- Generate Ideas
- Intellectual Property
- Life Sciences
- Materials
- Tech Scout
- Unparalleled Data Quality
- Higher Quality Content
- 60% Fewer Hallucinations
Browse by: Latest US Patents, China's latest patents, Technical Efficacy Thesaurus, Application Domain, Technology Topic, Popular Technical Reports.
© 2025 PatSnap. All rights reserved.Legal|Privacy policy|Modern Slavery Act Transparency Statement|Sitemap|About US| Contact US: help@patsnap.com