Heat pipe seal method
A sealing and heat pipe technology, applied in the field of heat pipe sealing, can solve problems such as increasing defective products, affecting product quality, and difficult operation, and achieve the effects of improving the good rate, reducing the time required for sealing, and increasing the heat conduction speed
- Summary
- Abstract
- Description
- Claims
- Application Information
AI Technical Summary
Problems solved by technology
Method used
Image
Examples
Embodiment
[0024] Example: see Figure 3A , 3B , 3C, 3D, the step diagram of heat pipe sealing method provided by the present invention, its sealing method is as follows:
[0025] Step 1: If Figure 3A As shown, take the heat pipe 1 first, and turn a small section of the opening end of the heat pipe 1 into an extension section 11 with a smaller aperture, so that the diameter of the opening end is smaller than the diameter of the heat pipe 1, so as to facilitate heat conduction The addition of liquid and the extraction of air cause the heat pipe 1 to maintain a vacuum state, and through the small diameter of the extension section 11, it is difficult for air to enter the heat pipe 1 when the heat pipe 1 is sealed;
[0026] Step 2: If Figure 3B As shown, the extension section 11 of the heat pipe 1 is rotated and extruded through the mold, so that the tube wall of the extension section 1 is completely sealed by the continuous rotation and extrusion of the mold;
[0027] Step 3: If Fig...
PUM
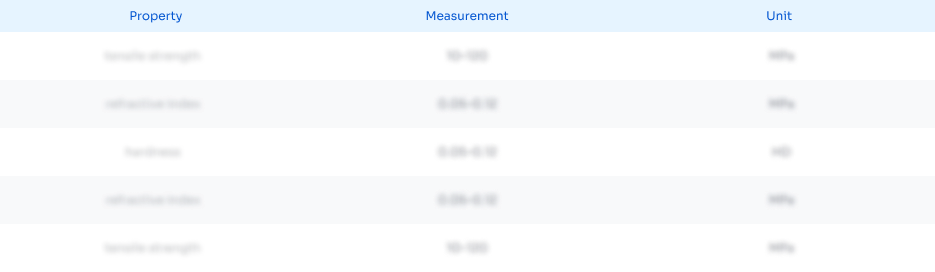
Abstract
Description
Claims
Application Information

- R&D
- Intellectual Property
- Life Sciences
- Materials
- Tech Scout
- Unparalleled Data Quality
- Higher Quality Content
- 60% Fewer Hallucinations
Browse by: Latest US Patents, China's latest patents, Technical Efficacy Thesaurus, Application Domain, Technology Topic, Popular Technical Reports.
© 2025 PatSnap. All rights reserved.Legal|Privacy policy|Modern Slavery Act Transparency Statement|Sitemap|About US| Contact US: help@patsnap.com