Treatment technique for acid washing surface of electronic rotor
A treatment process and a technology for motor rotors, which are applied in the field of pickling treatment process and motor rotor surface pickling treatment process, can solve the problems of increasing rotor core loss and load stray loss, reducing motor efficiency, reducing contact resistance, etc. Achieve the effect of reducing stray loss and improving efficiency
- Summary
- Abstract
- Description
- Claims
- Application Information
AI Technical Summary
Problems solved by technology
Method used
Image
Examples
Embodiment Construction
[0009] The present invention will be described in more detail below in conjunction with the accompanying drawings and embodiments.
[0010] refer to figure 1 , which is a flow chart of the pickling process of the present invention to greatly reduce the stray loss of the motor.
[0011] As shown in the figure, the surface pickling treatment process of the motor rotor, the process steps are:
[0012] First select the rotors whose efficiency test fails to meet the standard as the rotors for pickling. Then process them step by step:
[0013] The first step: remove the outer circle of the rotor by about 0.10mm;
[0014] The second step: mix hydrochloric acid and water into a 1:1 solution;
[0015] Step 3: Treat the outer surface of the rotor with hydrochloric acid solution and paint all over;
[0016] Step 4: Put the motor rotor that has been completely painted on the surface into an oven to dry for an unlimited time.
[0017] The minimum time limit for drying the treated moto...
PUM
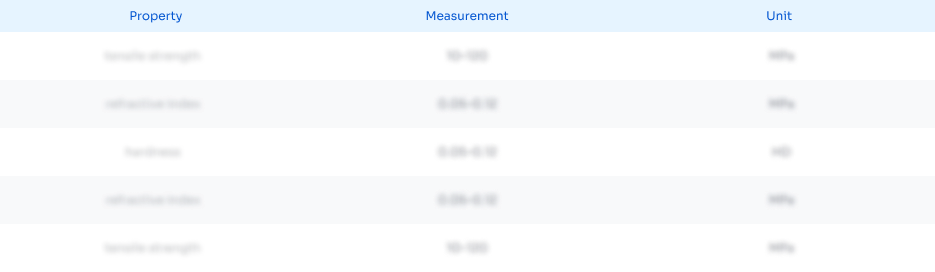
Abstract
Description
Claims
Application Information

- R&D
- Intellectual Property
- Life Sciences
- Materials
- Tech Scout
- Unparalleled Data Quality
- Higher Quality Content
- 60% Fewer Hallucinations
Browse by: Latest US Patents, China's latest patents, Technical Efficacy Thesaurus, Application Domain, Technology Topic, Popular Technical Reports.
© 2025 PatSnap. All rights reserved.Legal|Privacy policy|Modern Slavery Act Transparency Statement|Sitemap|About US| Contact US: help@patsnap.com