Method for forming magnesium alloy pipe fitting
A technology for magnesium alloys and pipe fittings, applied in the field of forming methods and devices for magnesium alloy pipe fittings, can solve the problems of complex pretreatment process, production of magnesium alloy pipes, affecting practicability, etc., achieve good comprehensive mechanical properties, improve material utilization, Easy-to-use effects
- Summary
- Abstract
- Description
- Claims
- Application Information
AI Technical Summary
Problems solved by technology
Method used
Image
Examples
Embodiment 1
[0024] as attached figure 1 As shown, this embodiment provides a superplastic forming process and device for magnesium alloy pipe fittings. The device is composed of a mold, a tube billet sealing mechanism, a pressure medium source and a heating mechanism. The mold is composed of an upper mold 1 and a lower mold 5. The lower end surface of the upper mold 1 and the end surface of the lower mold 5 have a mold cavity for bending the tube blank and providing bulging; the sealing mechanism is sealed on both sides of the upper and lower mold clamping parts. Plugs 3 and 4 (with air inlet holes) and hydraulic cylinders 7 and 8 are used to seal the tube blank; the pressure medium is compressed air, which is provided by a pressure conversion device composed of hydraulic cylinder (10) and cylinder (9); The heating mechanism is composed of an electric heating tube 6 placed inside the upper mold 1 and the lower mold 5 .
[0025] The forming process provided in this embodiment is as follo...
Embodiment 2
[0027] as attached figure 2 As shown, this embodiment provides a superplastic forming process and device for magnesium alloy pipe fittings. The device is composed of a mold, a tube billet sealing mechanism, a pressure medium source and a heating mechanism. The mold is composed of an upper mold 1 and a lower mold 5. The lower end surface of the upper mold 1 and the end surface of the lower mold 5 have a mold cavity for bending the tube blank and providing bulging; the sealing mechanism is sealed on both sides of the upper and lower mold clamping parts. Plugs 3, 4 and hydraulic cylinders 7, 8 are used to seal the tube blank; the pressure medium is pressure oil, which is directly taken from the oil supply system of the hydraulic machine and controlled by the reversing valve 12; the heating mechanism is composed of a low-pressure two-way pump 13, Heating oil tank 14 forms.
[0028] The forming process provided in this embodiment is as follows: put the AK60 magnesium alloy tube ...
PUM
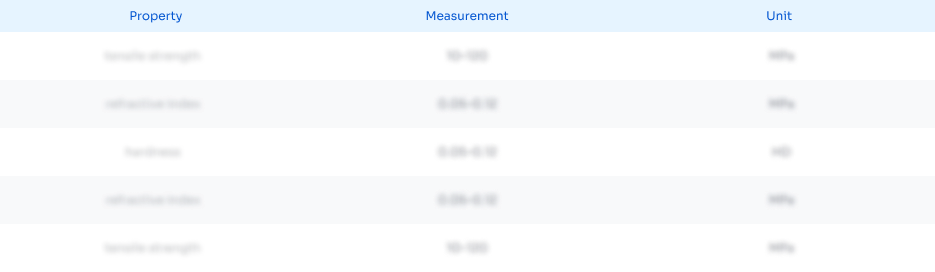
Abstract
Description
Claims
Application Information

- R&D
- Intellectual Property
- Life Sciences
- Materials
- Tech Scout
- Unparalleled Data Quality
- Higher Quality Content
- 60% Fewer Hallucinations
Browse by: Latest US Patents, China's latest patents, Technical Efficacy Thesaurus, Application Domain, Technology Topic, Popular Technical Reports.
© 2025 PatSnap. All rights reserved.Legal|Privacy policy|Modern Slavery Act Transparency Statement|Sitemap|About US| Contact US: help@patsnap.com