Novel composite material for blast pipe sheet
A composite material and air duct technology, applied in the field of new materials, can solve the problems of insufficient strength of aluminum foil polyurethane material, high cost of aluminum skin, easy rust of iron skin, etc.
- Summary
- Abstract
- Description
- Claims
- Application Information
AI Technical Summary
Problems solved by technology
Method used
Examples
Embodiment approach
[0012] Required equipment: 1. Reactor 2. Mixer 3. Foam barrel 4. JL-I sheet forming machine
[0013] Process:
[0014] 1. Pour 40kg of magnesium chloride, 50kg of water, and 0.3kg of ultramarine powder into the reaction pot and stir for 1 minute, then add 0.25kg of phosphoric acid and stir for 1 minute, then add 100kg of magnesium oxide, stir for 1 minute, then add 50kg of heavy calcium carbonate and stir until uniform spare.
[0015] 2. Put 0.3kg of foaming liquid in a foaming barrel, pour 10kg of water, and stir for about 5 minutes (when adding the foaming liquid, dissolve it with hot water and foam with water at the same time)
[0016] 3. Pour the foamed water into the reaction pot and stir for 15 minutes until it is completely stirred evenly.
[0017] 4. Slowly pour the prepared slurry into the JL-I sheet forming machine, add 4 layers of medium-alkali glass fiber reinforced cloth and flame-resistant polystyrene in turn, and automatically form it in the machine.
PUM
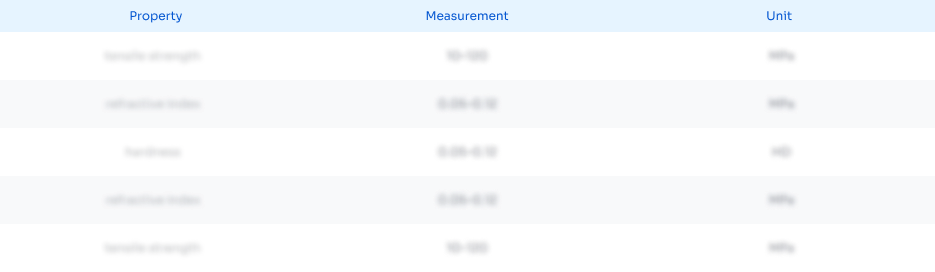
Abstract
Description
Claims
Application Information

- Generate Ideas
- Intellectual Property
- Life Sciences
- Materials
- Tech Scout
- Unparalleled Data Quality
- Higher Quality Content
- 60% Fewer Hallucinations
Browse by: Latest US Patents, China's latest patents, Technical Efficacy Thesaurus, Application Domain, Technology Topic, Popular Technical Reports.
© 2025 PatSnap. All rights reserved.Legal|Privacy policy|Modern Slavery Act Transparency Statement|Sitemap|About US| Contact US: help@patsnap.com