Ceramic co-fired type common mode filter and its making method
A common-mode filter and co-firing technology, which is applied to waveguide devices, inductors, fixed inductors, etc., can solve the problems of high differential-mode impedance, low cost, and large signal loss, achieving reduced impedance value and excellent performance , the effect of high impedance values
- Summary
- Abstract
- Description
- Claims
- Application Information
AI Technical Summary
Problems solved by technology
Method used
Image
Examples
Embodiment Construction
[0019] Relevant detailed content and technical description of the present invention, now in conjunction with accompanying drawing, explain as follows:
[0020] Please also see Figure 3-1 and Figure 3-2 As shown, they are respectively a three-dimensional schematic diagram and a cross-sectional view of the structure of the ceramic co-fired common mode filter of the present invention. As shown in the figure, the ceramic co-fired common mode filter 20 of the present invention is a coil-shaped inner electrode 21 and Two or more materials such as non-magnetic material 23 and magnetic material 22 are co-fired, and different parts of the components are selected according to the electrical requirements, and different materials are prepared according to the powder characteristics of the materials. Appropriate operability, so that the ceramic co-fired common-mode filter 20 of the main body is completed by co-firing through the special sintering curve that is produced together in each ...
PUM
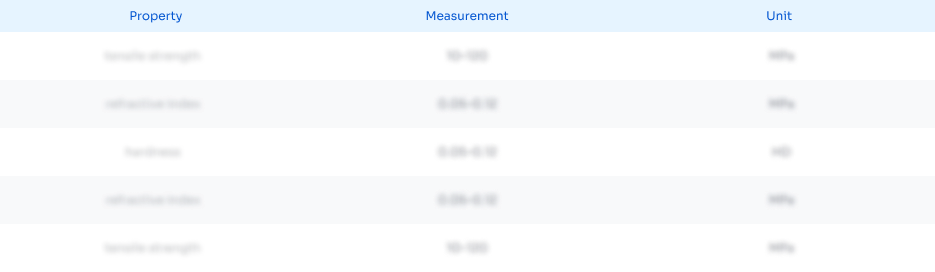
Abstract
Description
Claims
Application Information

- R&D Engineer
- R&D Manager
- IP Professional
- Industry Leading Data Capabilities
- Powerful AI technology
- Patent DNA Extraction
Browse by: Latest US Patents, China's latest patents, Technical Efficacy Thesaurus, Application Domain, Technology Topic, Popular Technical Reports.
© 2024 PatSnap. All rights reserved.Legal|Privacy policy|Modern Slavery Act Transparency Statement|Sitemap|About US| Contact US: help@patsnap.com