Method for producing ecological architectural material using sludge and gangue
A technology of ecological building and coal gangue, which is applied in the field of using sludge and coal gangue to produce ecological building materials, can solve the problems of serious secondary pollution and environmental impact, and achieve the effects of low production cost, energy saving, and significant economic benefits
- Summary
- Abstract
- Description
- Claims
- Application Information
AI Technical Summary
Problems solved by technology
Method used
Image
Examples
Embodiment 1
[0021] Embodiment 1: the method for making unburned brick:
[0022] Sludge is directly mixed with calcined or spontaneously combusted coal gangue to make unburned bricks. The specific steps are:
[0023] 1. Dry the dewatered sludge;
[0024] 2. Crushing coal gangue through three stages of coarse, medium and fine, until the content of particles less than 2mm is greater than 85%;
[0025] 3. Put the crushed gangue slag into the calciner and calcinate at a temperature of about 750°C for 8-10 hours to increase its activity (spontaneous combustion of gangue can be avoided);
[0026] 4. Put the coal gangue slag into hydrochloric acid or sulfuric acid acid solution for acid leaching for 4 hours; the leaching solution is filtered, crystallized, and polymerized to produce polyaluminium chloride or polyaluminum sulfate inorganic polymer flocculant; the leached gangue slag and the dried sludge mix. The weight percentage of the sludge is 12%-18%, and the coal gangue slag is 82%-88%. ...
Embodiment 2
[0029] Example 2: Sintered bricks are made by mixing sludge and gangue. The specific steps are: 1.
[0030] 1. Dry the dewatered sludge;
[0031] 2. The coal gangue mined in the coal mine is crushed and screened with a 2mm vibrating screen;
[0032] 3. Mixing the sieved coal gangue powder with dry sludge, the weight percentage of sludge is 15%-20%, and the weight percentage of coal gangue is 80%-85%;
[0033] 4. Add water, high-alumina cement, sodium carbonate and other external additives to the mixture of sludge and coal gangue powder and stir. Add 150kg-180kg of high-alumina cement, 150kg of water, 5kg of sodium carbonate, and 3kg of water reducing agent per ton of the mixture. After being stirred evenly for the second time, the mixture was made and aged for 2 hours;
[0034] 5. After aging, the mixture is placed in a pressure molding machine and pressed to form bricks, with a molding pressure of 5 tons;
[0035] 6. After the green body is dried at 110°C for 12 hours, pu...
Embodiment 3
[0036] Example 3: Mixing sludge and coal gangue to produce ceramsite. The specific steps are:
[0037] 1. Dry the dewatered sludge;
[0038] 2. The coal gangue mined in the coal mine is crushed and screened with a 2mm vibrating screen;
[0039] 3. Mixing the screened coal gangue powder with dry sludge, the weight percentage of sludge is 40%, and the weight percentage of coal gangue is 60%;
[0040] 4. Add high-alumina cement, water, sodium carbonate and other admixtures to the mixture of sludge and coal gangue powder and stir. Add 150-180kg of high-alumina cement, 150kg of water, 5kg of sodium carbonate, and 3kg of water reducer per ton of the mixture. After stirring for the first time, the mixture was made and aged for 2 hours;
[0041] 5. After aging, put the mixture into a disc granulator to make ceramsite body;
[0042] 6. After the ceramsite body is dried at 110°C for 12 hours, it is put into a calciner for calcination. The calcination temperature is about 1200°C, and...
PUM
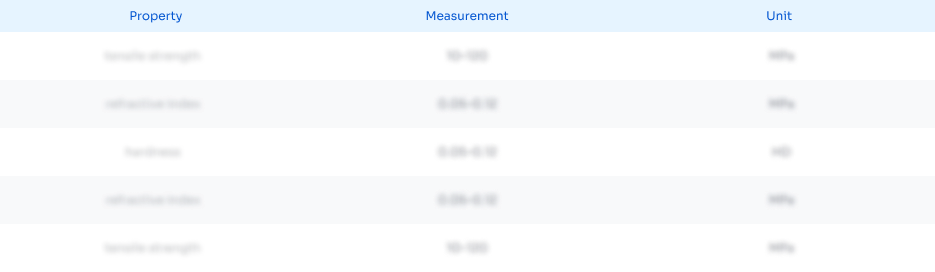
Abstract
Description
Claims
Application Information

- R&D
- Intellectual Property
- Life Sciences
- Materials
- Tech Scout
- Unparalleled Data Quality
- Higher Quality Content
- 60% Fewer Hallucinations
Browse by: Latest US Patents, China's latest patents, Technical Efficacy Thesaurus, Application Domain, Technology Topic, Popular Technical Reports.
© 2025 PatSnap. All rights reserved.Legal|Privacy policy|Modern Slavery Act Transparency Statement|Sitemap|About US| Contact US: help@patsnap.com