Brushless DC electric machine in structure of short magnetic circuit
A brushed DC motor, short magnetic circuit technology, applied in the magnetic circuit shape/style/structure, motor, magnetic circuit static parts and other directions, can solve the problems of limiting motor efficiency, large stator iron loss, affecting current control accuracy, etc.
- Summary
- Abstract
- Description
- Claims
- Application Information
AI Technical Summary
Problems solved by technology
Method used
Image
Examples
specific Embodiment approach 1
[0005] Specific implementation mode one: in conjunction with Fig. 1, figure 2 and image 3 Describe this specific embodiment, this specific embodiment is made up of stator 4, a plurality of permanent magnets 1, rotor 2, excitation winding 3; Stator 4 is a cylindrical sleeve, rotor 2 is a cylindrical tube; And take the rotation axis of the rotor 2 as the central axis to be evenly spaced from each other, the length direction of each permanent magnet 1 is parallel to the axis of the rotor 2 and the length of the permanent magnet 1 runs through the outer surface of the cylinder of the rotor 2; the stator 4 are set on the outside of the rotor 2, and an air gap 5 is left between the inner surface of the cylindrical sleeve of the stator 4 and the outer surface of the permanent magnet 1, and the axis line of the stator 4 coincides with the rotation axis of the rotor 2; the stator 4 There are a plurality of wide grooves 4-2 and narrow grooves 4-3 on the inner surface of the cylindrica...
specific Embodiment approach 2
[0006] Specific implementation mode two: combination Figure 4 and Figure 5 Describe this specific embodiment. The difference between this specific embodiment and specific embodiment 1 is that there are a plurality of deep grooves 2-1 uniformly opened on the outer cylindrical surface of the rotor 2, and each deep groove 2-1 is embedded with a The permanent magnet 1 adopts tangential magnetization, and the N pole and the S pole of the permanent magnet 1 are respectively connected to the two vertical walls of the deep groove 2-1; the center distance between every two adjacent deep grooves 2-1 The length of L3 is equal to the width L1 of the wide slot 4-2 on the stator 4.
PUM
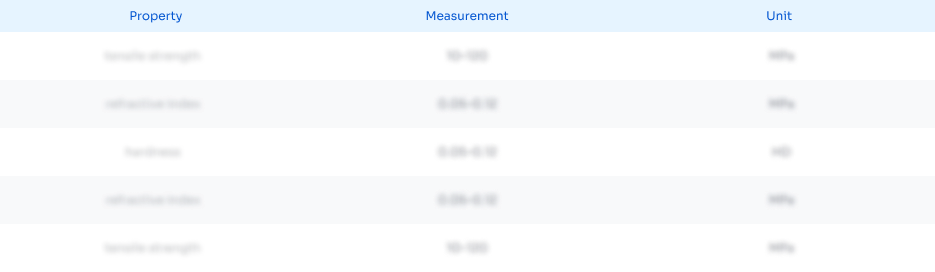
Abstract
Description
Claims
Application Information

- R&D
- Intellectual Property
- Life Sciences
- Materials
- Tech Scout
- Unparalleled Data Quality
- Higher Quality Content
- 60% Fewer Hallucinations
Browse by: Latest US Patents, China's latest patents, Technical Efficacy Thesaurus, Application Domain, Technology Topic, Popular Technical Reports.
© 2025 PatSnap. All rights reserved.Legal|Privacy policy|Modern Slavery Act Transparency Statement|Sitemap|About US| Contact US: help@patsnap.com