Polishing piece, polishing lap, and method of polishing glass panel for CRT
A grinding block and grinding disc technology, applied in abrasives, metal processing equipment, manufacturing tools, etc., can solve problems such as work efficiency, poor personnel efficiency, air pollution, and increased cost, and achieve high installation work efficiency and strong adhesion. , to ensure the effect of adhesion
- Summary
- Abstract
- Description
- Claims
- Application Information
AI Technical Summary
Problems solved by technology
Method used
Image
Examples
Embodiment Construction
[0051] exist figure 1 In , the circular grinding disc 1 , alignment template 2 , and pressing auxiliary plate 3 in the present invention are shown as rough grinding discs on the surface of an aspherical glass panel for a cathode ray tube.
[0052] The grinding disc 1 consists of a lowermost rigid non-woven base layer 4 made of nylon fibers, a soft elastic base layer 5 made of sponge as an intermediate layer, and a base layer 7 formed of a block mounting layer 6 made of rigid polyurethane as the upper layer. and a plurality of cylindrical grinding blocks 8 fixed on substantially the entire surface of the upper surface of the block mounting layer 6 at predetermined intervals by an adhesive layer.
[0053] Moreover, the grinding disc 1 is passed through screws (not shown) that can be inserted into a plurality of threaded holes 9 and a threaded hole 10 formed in the center portion of the hard non-woven fabric base layer 4. , connected with the disc rotation drive mechanism (not ...
PUM
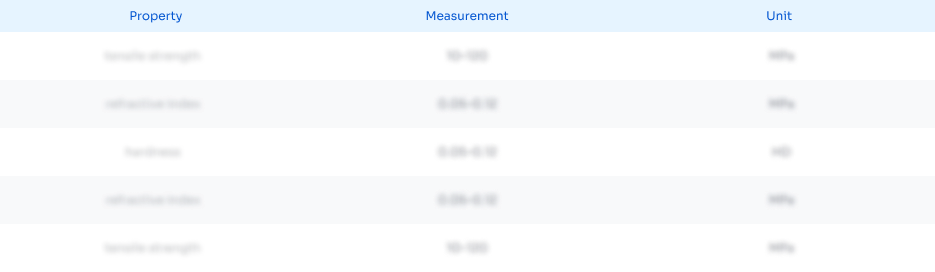
Abstract
Description
Claims
Application Information

- R&D
- Intellectual Property
- Life Sciences
- Materials
- Tech Scout
- Unparalleled Data Quality
- Higher Quality Content
- 60% Fewer Hallucinations
Browse by: Latest US Patents, China's latest patents, Technical Efficacy Thesaurus, Application Domain, Technology Topic, Popular Technical Reports.
© 2025 PatSnap. All rights reserved.Legal|Privacy policy|Modern Slavery Act Transparency Statement|Sitemap|About US| Contact US: help@patsnap.com