Rolling and hot melting process of producing integral plastic draining belt for reinforcing soft foundation
A technology of soft base reinforcement and manufacturing technology, which is applied to belts, other household appliances, household appliances, etc., can solve the problems of filter cloth strength reduction, shared external force, and filter sleeve breakage, etc. The effect of high lateral buckling capacity and good overall performance
- Summary
- Abstract
- Description
- Claims
- Application Information
AI Technical Summary
Problems solved by technology
Method used
Image
Examples
Embodiment Construction
[0008] Control attached Figure , Its process steps are divided into (1) the dried and stirred core board material is put into the extruder 1, (2) a flat plate is formed during extrusion, and the core board is calendered by the core board calender device (2) The ribs are shaped to form a filter element with a ribbed drainage channel; (3) After the core plate is shaped, it will be combined and positioned in the traction equipment 3 and 4 with the filter cloth sent by the filter cloth unwinding device and then sent to the hot rolling equipment 5 simultaneously. (4) The hot-melt composite of the filter membrane and the core plate is carried out in the hot rolling equipment to form a whole, (5) The size printing and slitting device 7 is divided into the corresponding width of the integral plastic drainage belt according to the required width of the produced product Mark the length and size, (6) send it to the finished product winding drum 9 for finished product winding, (7) the packagi...
PUM
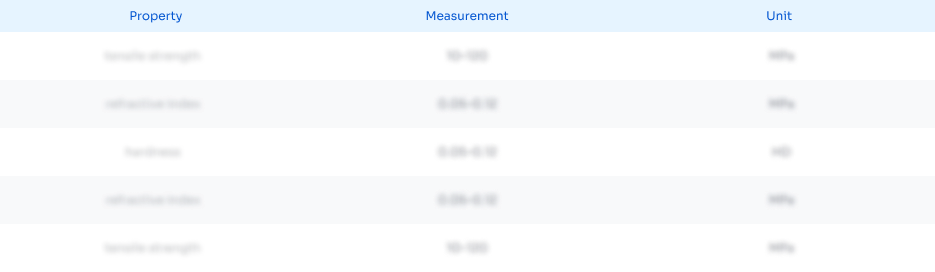
Abstract
Description
Claims
Application Information

- R&D
- Intellectual Property
- Life Sciences
- Materials
- Tech Scout
- Unparalleled Data Quality
- Higher Quality Content
- 60% Fewer Hallucinations
Browse by: Latest US Patents, China's latest patents, Technical Efficacy Thesaurus, Application Domain, Technology Topic, Popular Technical Reports.
© 2025 PatSnap. All rights reserved.Legal|Privacy policy|Modern Slavery Act Transparency Statement|Sitemap|About US| Contact US: help@patsnap.com