Quick calibrating method for line structure optical sensor based on coplanar calibrated reference
A calibration method and a technology of reference objects, which are applied in the field of optical vision measurement, can solve the problems that the number of calibration points cannot be too large, the planes block each other, and it is difficult to obtain high-quality calibration images, so as to improve calibration efficiency, reduce calibration intensity, and reduce cost effect
- Summary
- Abstract
- Description
- Claims
- Application Information
AI Technical Summary
Problems solved by technology
Method used
Image
Examples
Embodiment approach
[0021] like figure 1 As shown, the standard coplanar calibration reference object consists of a plane with good flatness and a plurality of circular holes on the plane, and the spatial relationship between the circular holes is known.
[0022] like figure 2 Shown: A standard coplanar calibration reference object containing multiple circular holes is placed in the measurement space of the online structured light sensor. When calibrating, first place the reference object at position i, get the projections of multiple circular holes on the image plane of camera C, and determine the coplanar reference object according to the image coordinates of the circular holes on the camera and the known spatial relationship. The plane equation of the surface reference object in the camera coordinate system (position i). At the same time, the light projector P produces a projection on the coplanar reference object ( figure 2 The solid line shown in the middle position i), and thus the ima...
PUM
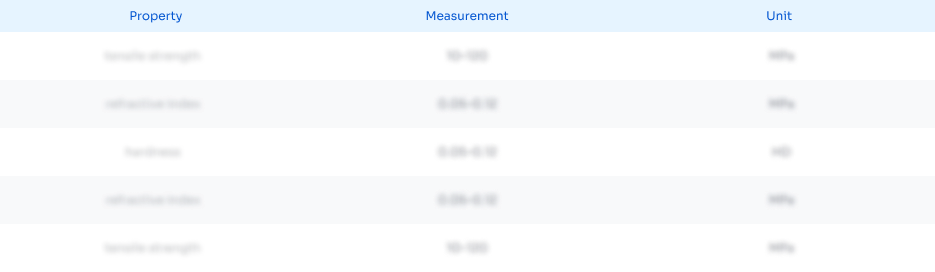
Abstract
Description
Claims
Application Information

- R&D
- Intellectual Property
- Life Sciences
- Materials
- Tech Scout
- Unparalleled Data Quality
- Higher Quality Content
- 60% Fewer Hallucinations
Browse by: Latest US Patents, China's latest patents, Technical Efficacy Thesaurus, Application Domain, Technology Topic, Popular Technical Reports.
© 2025 PatSnap. All rights reserved.Legal|Privacy policy|Modern Slavery Act Transparency Statement|Sitemap|About US| Contact US: help@patsnap.com