Thermal fatigue test device of piston
A test device and thermal fatigue technology, applied in the direction of measuring device, mechanical component testing, machine/structural component testing, etc. The effect of consistent temperature status and guaranteed reliability
- Summary
- Abstract
- Description
- Claims
- Application Information
AI Technical Summary
Problems solved by technology
Method used
Image
Examples
Embodiment Construction
[0026] The specific implementation manners of the present invention will be described in detail below in conjunction with the accompanying drawings, but it is not intended to limit the present invention.
[0027] Such as Figure 1-3As shown, a piston thermal fatigue test device includes a support frame 1 and a non-standard piston tooling 6 arranged on the support frame 1, a tested piston 4, a cooling water branch pipe 3, a heat shield, and a cooling water main pipe 2; After the test piston 4 is assembled with the piston ring, put it into the non-standard piston tooling 6. The cooling water main pipe 2 includes the cooling water inlet main pipe and the cooling water outlet main pipe. Some of the water inlets and outlets of the external thread are connected to the cooling water branch pipe 3, and the remaining water inlets and outlets of the external thread are sealed by the internal thread plug 5. Both the non-standard piston tooling and the tested piston have a cooling water i...
PUM
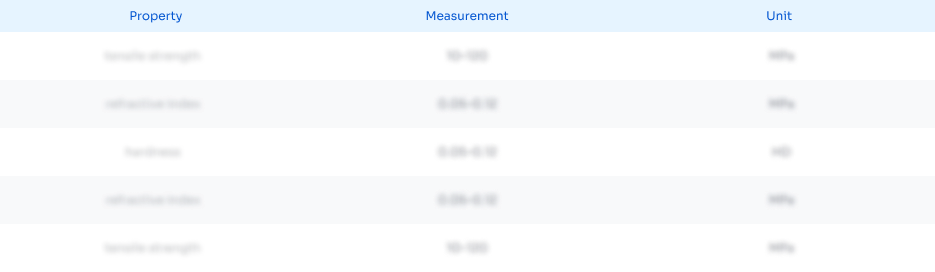
Abstract
Description
Claims
Application Information

- R&D
- Intellectual Property
- Life Sciences
- Materials
- Tech Scout
- Unparalleled Data Quality
- Higher Quality Content
- 60% Fewer Hallucinations
Browse by: Latest US Patents, China's latest patents, Technical Efficacy Thesaurus, Application Domain, Technology Topic, Popular Technical Reports.
© 2025 PatSnap. All rights reserved.Legal|Privacy policy|Modern Slavery Act Transparency Statement|Sitemap|About US| Contact US: help@patsnap.com