Styrene block copolymer reacting and extruding polymerization
A block copolymer and styrene-based technology, which is applied in the field of preparation of styrene-based block copolymers, can solve problems such as increased environmental protection pressure, high cost, and increased solvent separation
- Summary
- Abstract
- Description
- Claims
- Application Information
AI Technical Summary
Problems solved by technology
Method used
Examples
Embodiment 1
[0074] Refrigerate the styrene monomer and butadiene monomer that have been refined and treated to meet the polymerization requirements of the present invention to -10°C, and are transported to the mixing tank successively according to the weight ratio of styrene / butadiene = 70 / 30 under the delivery of a metering pump. Monomer storage tank, and make the two fully mixed evenly. Three feeding ports are set on the twin-screw extruder, which are the above-mentioned mixed monomer feeding port, tert-butyllithium initiator feeding port, and styrene monomer feeding port in turn; under the delivery of the metering pump, the refined The passed monomer and initiator are input into a twin-screw extruder for staged feeding reaction extrusion polymerization to obtain a block copolymer product A having a structure of styrene / butadiene-styrene with a number average molecular weight of 230,000.
[0075] The process conditions are set as follows:
[0076] The temperature of each section of the...
Embodiment 2
[0082] 4 feeding inlets are set on the twin-screw extruder, followed by chlorostyrene monomer feeding inlet, n-butyllithium initiator feeding inlet, chlorostyrene / butadiene mixed monomer (chlorobenzene Ethylene / butadiene=70 / 30) feed port, chlorostyrene monomer feed port; under the delivery of the metering pump, the refined monomer and initiator are input into the twin-screw extruder for staged feeding Reactive extrusion polymerization reaction to obtain a block copolymer product B with a number average molecular weight of 330,000 and a structure of chlorostyrene-chlorostyrene / butadiene-chlorostyrene.
[0083] The process conditions are set as follows:
[0084] The temperature of each section of the screw: 40 / 50 / 110 / 190 / 220 / 220°C
[0085] Monomer mass flow rate (kg / hour): chlorostyrene / mixed monomer / chlorostyrene=0.5 / 4.0 / 0.5
[0086] Initiator mass flow rate 1.2g / hour
[0087] Screw speed: 60 rpm.
[0088] product
Embodiment 3
[0090] 4 feed ports are set on the twin-screw extruder, followed by styrene monomer feed port, isopropyllithium initiator feed port, butadiene / isoprene mixed monomer (butadiene / isoprene) Pentadiene=50 / 50) feed port, styrene monomer feed port; under the delivery of the metering pump, the refined monomer and initiator are input into the twin-screw extruder for staged feeding reaction extrusion polymerization Reaction, the structure of styrene-butadiene / isoprene-styrene multi-block copolymer product C with a number average molecular weight of 320,000 was obtained.
[0091] The process conditions are set as follows:
[0092] The temperature of each section of the screw: 50 / 80 / 180 / 200 / 200 / 200°C
[0093] Monomer mass flow rate (kg / hour): styrene / mixed monomer / styrene=2.0 / 1.5 / 2.5
[0094] Initiator mass flow rate 1.2g / hour
[0095] product
PUM
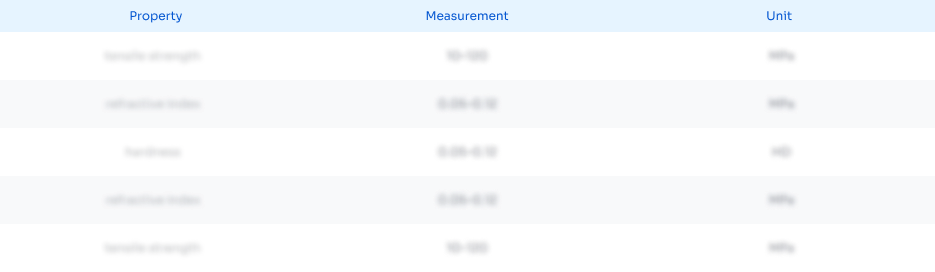
Abstract
Description
Claims
Application Information

- R&D
- Intellectual Property
- Life Sciences
- Materials
- Tech Scout
- Unparalleled Data Quality
- Higher Quality Content
- 60% Fewer Hallucinations
Browse by: Latest US Patents, China's latest patents, Technical Efficacy Thesaurus, Application Domain, Technology Topic, Popular Technical Reports.
© 2025 PatSnap. All rights reserved.Legal|Privacy policy|Modern Slavery Act Transparency Statement|Sitemap|About US| Contact US: help@patsnap.com