Reactor combustion control method and reactor
A control method and technology of a reaction furnace, applied in the direction of combustion method, combustion type, combustion equipment, etc., can solve the problems of reaction tube heat (reduced heat transfer efficiency, lack of uniformity in heating, etc.), to reduce temperature difference and yield little effect
- Summary
- Abstract
- Description
- Claims
- Application Information
AI Technical Summary
Problems solved by technology
Method used
Image
Examples
Embodiment Construction
[0039] Hereinafter, embodiments of the present invention will be described in detail with reference to the drawings. figure 1 It is a figure which shows the schematic structure of an example of embodiment of the reforming reaction furnace which used this invention for a test. figure 1 Among them, the mark 1 indicates the furnace body with the combustion chamber 2 inside. The furnace body 1 is provided with a bottom wall (hearth) 1a and an upper wall (roof) 1b constituting a pair of wall portions, constituting a width direction (from figure 1 The sidewalls 1c and 1d of a pair of wall parts, which are seen as being perpendicular to the front-rear direction of the paper surface, constitute the lateral direction (from figure 1 See side walls 1e and 1f of a pair of wall portions in the left-right direction).
[0040] The bottom wall (hearth) 1a of the furnace body 1 is supported by a support structure not shown in the figure. On the upper wall (furnace roof) 1b of the furnace ma...
PUM
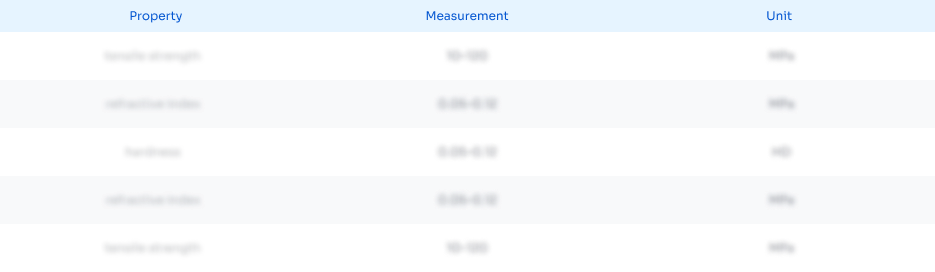
Abstract
Description
Claims
Application Information

- R&D
- Intellectual Property
- Life Sciences
- Materials
- Tech Scout
- Unparalleled Data Quality
- Higher Quality Content
- 60% Fewer Hallucinations
Browse by: Latest US Patents, China's latest patents, Technical Efficacy Thesaurus, Application Domain, Technology Topic, Popular Technical Reports.
© 2025 PatSnap. All rights reserved.Legal|Privacy policy|Modern Slavery Act Transparency Statement|Sitemap|About US| Contact US: help@patsnap.com