An Al-Mo-V intermediate alloy and process for preparing same
A master alloy, aluminum-molybdenum technology, applied in the field of aluminum-molybdenum-vanadium master alloy and its preparation, can solve the problems of unsatisfactory diversification, high cost, narrow adaptability, etc., and achieve easy storage and transportation, low cost, and low production cost Effect
- Summary
- Abstract
- Description
- Claims
- Application Information
AI Technical Summary
Problems solved by technology
Method used
Image
Examples
Embodiment 1
[0016] Using the ignition smelting method outside the furnace: according to the conventional steps, the raw materials are dried, the furnace is built, the ingredients are prepared according to the weight percentage, the materials are evenly mixed, the furnace is loaded, smelted, cooled, the furnace is started, weighing, finishing, crushing, magnetic Selection, sampling analysis, packaging.
[0017] Concrete preparation process is as follows:
[0018] 1. Drying of raw materials: drying raw materials, masonry slag, and batching slag in a drying room at a temperature of 75°C (can be 75±5°C) for 24 hours (can be 24 to 72 hours);
[0019] 2. Weigh raw materials: Potassium chlorate is used as a catalyst during batching (adding weight is 5-15% of the total amount of raw materials)
[0020] Al V 2 o 5 MoO 3 CaF 2 KClO 3
[0021] 1kg 0.189kg 0.159kg 0.117kg 0.151kg
[0022] 3. Mixing: put the material into the V-shaped mixer, mix evenly, and the number of times is 6 times...
Embodiment 2~4
[0034] Embodiment 2~4. Operate by the method of embodiment 1, see table 1 with embodiment 1 difference.
[0035] Table 1. Reaction system of aluminum molybdenum vanadium alloy
[0036]
PUM
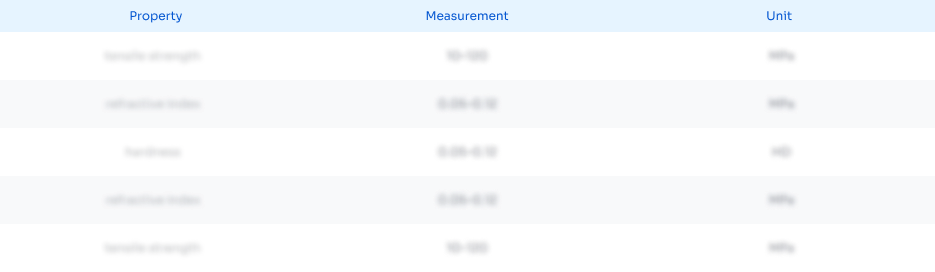
Abstract
Description
Claims
Application Information

- R&D
- Intellectual Property
- Life Sciences
- Materials
- Tech Scout
- Unparalleled Data Quality
- Higher Quality Content
- 60% Fewer Hallucinations
Browse by: Latest US Patents, China's latest patents, Technical Efficacy Thesaurus, Application Domain, Technology Topic, Popular Technical Reports.
© 2025 PatSnap. All rights reserved.Legal|Privacy policy|Modern Slavery Act Transparency Statement|Sitemap|About US| Contact US: help@patsnap.com