Hot-rolled patterned steel sheet production method
A production method and patterned plate technology, applied in the field of hot-rolled plate production technology, can solve the problems of high rolling pressure, difficult to control plate shape, affecting output and quality, etc., and achieve a good plate shape, beautiful appearance and improved quality. Effect
- Summary
- Abstract
- Description
- Claims
- Application Information
AI Technical Summary
Problems solved by technology
Method used
Examples
Embodiment 1
[0011] Embodiment 1: adopt following concrete process method when rolling checkered plate:
[0012] 1. Descaling system: 1 set of VSB rollers, 1 set of R1 rollers, 1 set of F0 rollers;
[0013] 2. The exit temperature of rough rolling is controlled at 1100°C;
[0014] 3. The exit temperature of finish rolling is controlled at 900°C;
[0015] 4. The cooling water between the finishing stands is closed;
[0016] 5. The engraving depth of the pattern roller increases from 2.8mm to 4mm.
[0017] Adopting the pattern roll stand of the present invention, the reduction rate is reduced to 14%, and the pattern plate rolled out has a beautiful appearance, and the height of the pattern exceeds 20% of the base plate, which meets the national standard; because the reduction rate is similar to that of rolling a flat plate, the plate shape is relatively small. Good; the rolling pressure is significantly reduced, and the minimum production thickness can reach 2.5mm; the rolling shift produ...
Embodiment 2
[0018] Example 2: The exit temperature of rough rolling is controlled at 1070°C; the exit temperature of finish rolling is controlled at 890°C; the reduction rate is 13%, and the rest are the same as in Example 1.
PUM
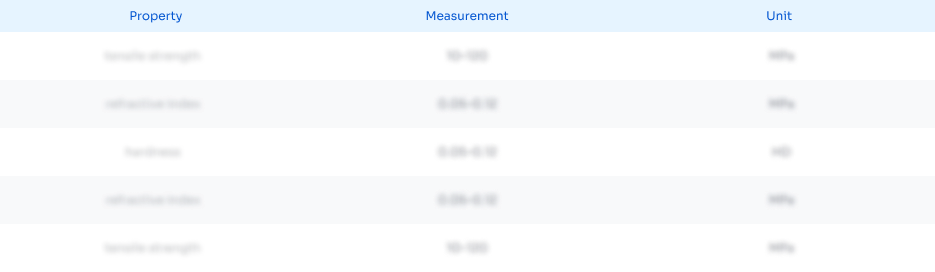
Abstract
Description
Claims
Application Information

- R&D
- Intellectual Property
- Life Sciences
- Materials
- Tech Scout
- Unparalleled Data Quality
- Higher Quality Content
- 60% Fewer Hallucinations
Browse by: Latest US Patents, China's latest patents, Technical Efficacy Thesaurus, Application Domain, Technology Topic, Popular Technical Reports.
© 2025 PatSnap. All rights reserved.Legal|Privacy policy|Modern Slavery Act Transparency Statement|Sitemap|About US| Contact US: help@patsnap.com