Filter material of gradient distribution and its preparation process
A filter material and gradient distribution technology, applied in the field of filter materials, can solve the problems of high cost, unfavorable filtration, and inability to give full play to hybrid fibers, and achieve the effects of excellent performance, improved service life and low cost
- Summary
- Abstract
- Description
- Claims
- Application Information
AI Technical Summary
Problems solved by technology
Method used
Image
Examples
Embodiment 1
[0043] Embodiment 1: A kind of gradient distribution fiber filter material, containing coniferous wood pulp, polypropylene fiber, dispersant NP-6, cationic polyacrylamide, red dye, bright yellow dye, modified vinyl acetate emulsion, its mass parts number becomes: 90 parts of softwood pulp, 10 parts of polypropylene fiber, 0.01 part of dispersant NP-6, 5 parts of cationic polyacrylamide, 0.6 parts of red dye, 1 part of bright yellow dye, 20 parts of modified vinyl acetate emulsion.
[0044] 1. The coniferous wood pulp is beaten to a beating degree of 15°SR, and then diluted to a concentration of 0.1% by weight;
[0045] 2. Disperse the polypropylene fiber in the NP-6 solution containing 0.01 part, the fiber concentration is 0.5% by weight, the length of the polypropylene fiber is 3 mm, and the width is 10 μm;
[0046] 3. Mix coniferous wood pulp and polypropylene fiber pulp, and adjust the concentration to 0.02%;
[0047] 4. Add 5 parts of cationic polyacrylamide
[0048] 5. ...
Embodiment 2
[0054]Example 2: A gradient distribution fiber filter material, containing mercerized wood pulp, hemp pulp, glass fiber, dispersant NP-10, polyethylene oxide, PPE, anionic polyacrylamide, dark green dye, bright yellow dye, modified benzene Acrylic emulsion, its mass parts array is: 15 parts of mercerized wood pulp, 15 parts of hemp pulp, 70 parts of glass fiber, 0.8 part of dispersant NP-10, 0.1 part of polyethylene oxide, 1 part of PPE, 0.1 part of anionic polyacrylamide ; 1 part of dark green dye, 2 parts of light yellow dye, 30 parts of modified styrene-acrylic emulsion.
[0055] 1. Beat mercerized wood pulp and hemp pulp separately to a beating degree of 16°SR, and then dilute to a concentration of 0.5%;
[0056] 2. Disperse the glass fibers in a mixed aqueous solution containing 0.8 parts of NP-10 and 0.02 parts of polyethylene oxide, the fiber concentration is 0.1%, the length of the glass fibers is 15 mm, and the width is 5 μm;
[0057] 3. Mix mercerized wood pulp, hem...
Embodiment 3
[0065] Example 3: A gradient distribution fiber filter material, containing composite fiber, polyester, ceramic fiber, dispersant NP-9, dispersant NP-6, carboxymethyl cellulose, blue dye, modified vinyl acetate and phenolic compound Resin, its mass parts array is: 30 parts of composite fiber, 20 parts of polyester, 50 parts of ceramic fiber, 0.1 part of dispersant NP-9, 0.5 part of dispersant NP-6, 0.2 part of carboxymethyl cellulose, 0.5 part of blue dye 10 parts, modified vinyl acetate and phenolic composite resin.
[0066] 1. The composite fiber is dispersed in a solution containing 0.1 part of NP-9, the fiber concentration is 0.2% by weight, the composite fiber is 10 mm long and 20 μm wide;
[0067] 2. Polyester fibers are dispersed in a solution containing 0.5 parts of NP-6, the fiber concentration is 0.3% by weight, and the polyester fibers are 15 mm long and 15 μm wide;
[0068] 3. The ceramic fiber is dispersed in an aqueous solution of carboxymethyl cellulose contain...
PUM
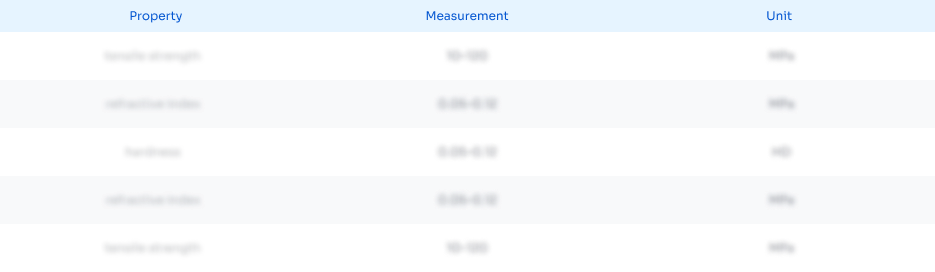
Abstract
Description
Claims
Application Information

- Generate Ideas
- Intellectual Property
- Life Sciences
- Materials
- Tech Scout
- Unparalleled Data Quality
- Higher Quality Content
- 60% Fewer Hallucinations
Browse by: Latest US Patents, China's latest patents, Technical Efficacy Thesaurus, Application Domain, Technology Topic, Popular Technical Reports.
© 2025 PatSnap. All rights reserved.Legal|Privacy policy|Modern Slavery Act Transparency Statement|Sitemap|About US| Contact US: help@patsnap.com