Process for extracting iron concentrate by sulfuric slag flotation
A process method and sulfuric acid slag technology, applied in the field of flotation process, can solve the problems of loss of economy, difficulty in fully meeting the quality requirements of iron concentrates, and low recovery rate, and achieve obvious resource utilization, high recovery rate, and land reduction. Effect
- Summary
- Abstract
- Description
- Claims
- Application Information
AI Technical Summary
Problems solved by technology
Method used
Image
Examples
Embodiment 1
[0014] 500 g of sulfuric acid slag with an iron grade of 49% is selectively ground in a rod mill with a grinding concentration of 20%, and the obtained grinding product has a particle size of -200 mesh of 70%. Add acidified water glass 1kg / t to the flotation machine and stir for 10 minutes, then add fatty acid collector 1.3kg / t and stir for 8 minutes to keep the flotation concentration at 50%, and finally add alcohol foaming agent 50g / t Stirring for 2 minutes, flotation for 7 minutes to obtain flotation rough concentrate. The rough concentrate is subjected to three times of beneficiation to obtain qualified iron concentrate. The three selected tailings are combined, and the iron concentrate and tailings are obtained by separate screening. The scavenging concentrate was combined with the concentrate III concentrate to obtain a final iron concentrate grade of 60.78%, a recovery rate of 74.84%, and a yield of 62.02%. The flotation tailings contain 19.91% iron and can be used as...
Embodiment 2
[0016] 500g of sulfuric acid slag with an iron grade of 48.2% is selectively ground in a rod mill with a grinding concentration of 50%, and the obtained grinding product has a particle size of -200 mesh of 86%. Add acidified water glass 1.6kg / t to the flotation machine and stir for 10 minutes, then add sulfonic acid collector 3kg / t and stir for 8 minutes to keep the flotation concentration at 30%, and finally add 50g of alcohol foaming agent / t Stirring for 2 minutes, flotation for 7 minutes to obtain flotation rough concentrate. The rough concentrate is subjected to three times of beneficiation to obtain qualified iron concentrate. The three selected tailings are combined, and the iron concentrate and tailings are obtained by separate screening. The scavenging concentrate is combined with the concentrate III concentrate to obtain a final iron concentrate grade of 61.52%, a recovery rate of 72.5%, and a yield of 60.3%. The flotation tailings contain 17.32% iron and can be us...
Embodiment 3
[0018] 500g of sulfuric acid slag with an iron grade of 49.3% is ground in a ball mill with a grinding concentration of 80%, and the obtained grinding product has a particle size of -200 mesh of 95%. Add acidified water glass 10kg / t to the flotation machine and stir for 10 minutes, then add sulfonic acid collector 5kg / t and stir for 8 minutes to keep the flotation concentration at 20%, and finally add alcohol foaming agent 50g / t Stirring for 2 minutes and flotation for 4 minutes to obtain flotation rough concentrate. The rough concentrate is subjected to three times of beneficiation to obtain qualified iron concentrate. The three selected tailings are combined, and the iron concentrate and tailings are obtained by separate screening. The scavenging concentrate was combined with the concentrate III concentrate to obtain a final iron concentrate grade of 60.92%, a recovery rate of 70.55%, and a yield of 58.3%. The flotation tailings contain 23.72% iron and can be used as cemen...
PUM
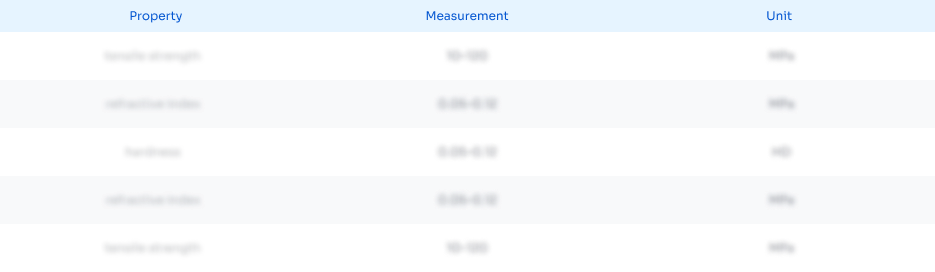
Abstract
Description
Claims
Application Information

- R&D
- Intellectual Property
- Life Sciences
- Materials
- Tech Scout
- Unparalleled Data Quality
- Higher Quality Content
- 60% Fewer Hallucinations
Browse by: Latest US Patents, China's latest patents, Technical Efficacy Thesaurus, Application Domain, Technology Topic, Popular Technical Reports.
© 2025 PatSnap. All rights reserved.Legal|Privacy policy|Modern Slavery Act Transparency Statement|Sitemap|About US| Contact US: help@patsnap.com