Polyurethane elastic floor brick and manufacturing method thereof
A technology of polyurethane elasticity and manufacturing method, applied in the direction of elastic floor and other directions, can solve the problems of complex raw materials, poor product elasticity, single structure, etc., and achieve the effects of good mechanical strength, good elasticity and good flame retardant effect.
- Summary
- Abstract
- Description
- Claims
- Application Information
AI Technical Summary
Problems solved by technology
Method used
Examples
Embodiment 1
[0019] A. Slowly and uniformly add 15kg of 4,4'-diphenylmethane diisocyanate into 85Kg polyoxypropylene diol at 60°C and stir to form a mixture, which is sealed at a constant temperature of 90°C for 1 hour to form a prepolymer thing;
[0020] B, 3kg of 1,4-butanediol is heated to a constant temperature of 90°C, after heating the prepolymer in A to 90°C, the two are mixed and stirred rapidly, and then 5kg of tris(β-chloroethyl)phosphate, Talcum powder 20kg stirring and mixing;
[0021] C. Pour the uniformly stirred mixture in step B into a 400mm×500mm, rectangular mold with a uniform columnar concave-convex structure, bake, and cool and demould after forming.
Embodiment 2
[0023] A. Slowly and uniformly add 25kg of 4,4'-diphenylmethane diisocyanate into 75kg of polyoxypropylene triol at 40°C and at the same time add blue polyurethane pigment to stir to form a mixture, and seal it at a constant temperature of 80°C Refined into prepolymer in 4 hours;
[0024] B, after heating the prepolymer in A to 80 DEG C, the calcium carbonate of tris (beta-chloropropyl) phosphate of 8kg and 50kg is mixed and stirred rapidly;
[0025] C. Pour the uniformly stirred mixture in step B into a 1000mm×1000mm, square mold with a flat bottom surface structure, bake, and cool and demould after forming.
Embodiment 3
[0027] A. Slowly and evenly add 10kg of 4,4'-diphenylmethane diisocyanate into 80°C, 90kg of polyoxypropylene triol and stir to form a mixture, and seal it at a constant temperature of 100°C for half an hour to form a prepolymer ;
[0028] B. Heat 15kg of 1,4-butanediol to a constant temperature of 110°C, heat the prepolymer in A to 110°C and mix and stir, then add 10kg of tris(2,3-dichloropropyl) phosphate and 30kg of talcum powder Quickly mix and stir;
[0029] C. First spread the transfer pattern in a 400mm×400mm, diamond-shaped, uniform dot-shaped concave-convex mold, and then pour the evenly stirred mixture in step B into it, bake it, and cool and demould after it is formed. .
PUM
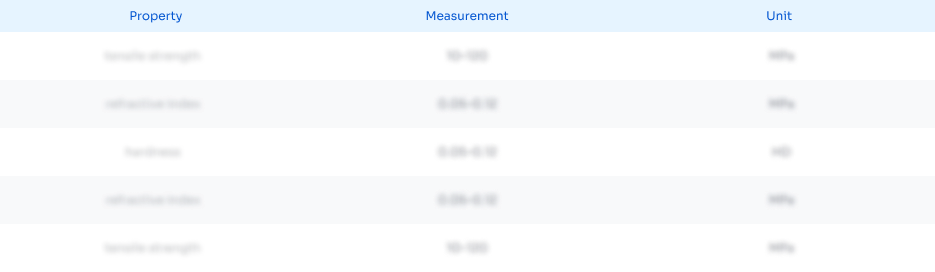
Abstract
Description
Claims
Application Information

- Generate Ideas
- Intellectual Property
- Life Sciences
- Materials
- Tech Scout
- Unparalleled Data Quality
- Higher Quality Content
- 60% Fewer Hallucinations
Browse by: Latest US Patents, China's latest patents, Technical Efficacy Thesaurus, Application Domain, Technology Topic, Popular Technical Reports.
© 2025 PatSnap. All rights reserved.Legal|Privacy policy|Modern Slavery Act Transparency Statement|Sitemap|About US| Contact US: help@patsnap.com