Carbon nanometer tube arc discharge preparation method under vacuum condition
A technology of arc discharge and carbon nanotubes, which is applied in petrochemical, carbon materials, and coal chemical industries. It can solve the problems of high cost of CNT, low degree of graphitization of CNT, and difficulty in large-scale production of CNT, and achieve mechanical and electronic properties. Good, less structural defects, lower production cost
- Summary
- Abstract
- Description
- Claims
- Application Information
AI Technical Summary
Problems solved by technology
Method used
Image
Examples
Embodiment 1
[0022] SWCNTs were prepared from coal by vacuum arc evaporation. First prepare the composite coal-based carbon rod mixed with the catalyst, the basic properties of the coal used are as follows: M ad = 2.34%, A d = 3.13%, V daf = 15.70%; C daf =87.21%, H daf =3.53%, N daf =1.06%. Take 500g of the raw coal sample, pulverize it in a pulverizer and sieve it until the particle size is less than 150μm, and dry it for later use. Take 200g of the above dry coal sample and mix it with 100g of coal tar and 5g of iron powder (the purity of the iron powder is 99.9%, and the particle size is less than 200μm) and put it into the mixer and stir evenly to obtain a viscous mixture, and then put this mixture into The mold is extruded into coal rods with a hydraulic press. The forming pressure is 10 MPa, the forming speed is 0.5 cm / s, and a coal rod with a diameter of 10 mm is obtained. The above-mentioned coal rods were cut off to make short rods with a length of 10 cm, and then put into...
Embodiment 2
[0025] MWCNTs were prepared from coal under vacuum discharge conditions. Get coal sample 200g (the analysis data of coal is the same as embodiment 1), pulverize and sieve to particle size and be less than 150 μ m, fully mix with coal tar; This mixture is compacted, carbonized, and preparation process is identical with embodiment 1. Put the prepared carbon rod into the arc device for arc discharge evaporation and gasification. Vacuumize, pass the cooling water, turn on the power, adjust the distance between the electrodes to stabilize the arc, and the entire discharge time lasts about 25 minutes; after the discharge is over, turn off the power and stop the cooling water. Opening the reactor revealed pencil-shaped MWCNTs growing from the cathode end of the reactor. The collected products were weighed and the yield was calculated. Under the above conditions, the yield of carbon nanotubes was 7g / h. The obtained carbon nanotube products were characterized and analyzed by high-res...
PUM
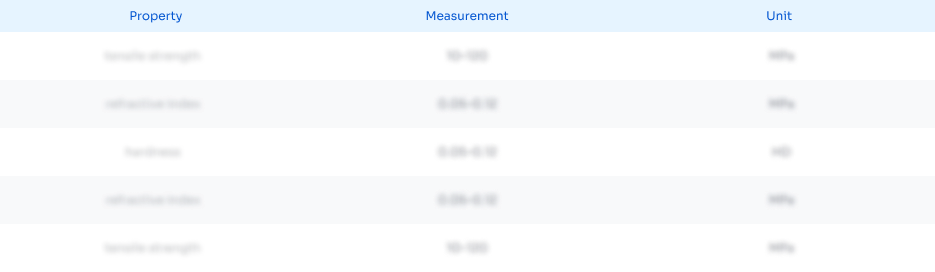
Abstract
Description
Claims
Application Information

- R&D Engineer
- R&D Manager
- IP Professional
- Industry Leading Data Capabilities
- Powerful AI technology
- Patent DNA Extraction
Browse by: Latest US Patents, China's latest patents, Technical Efficacy Thesaurus, Application Domain, Technology Topic, Popular Technical Reports.
© 2024 PatSnap. All rights reserved.Legal|Privacy policy|Modern Slavery Act Transparency Statement|Sitemap|About US| Contact US: help@patsnap.com