Stepwise grog burning furnace
A sintering furnace and clinker technology, applied in the field of sintering furnaces, can solve the problems of unstable sintering material quality, uneven sintering degree, poor sintering quality, etc., achieve simple structure, less auxiliary equipment, and improve heat exchange rate Effect
- Summary
- Abstract
- Description
- Claims
- Application Information
AI Technical Summary
Problems solved by technology
Method used
Image
Examples
Embodiment Construction
[0013] see figure 1 , the general shaft kiln type firing furnace includes a feeding port, a discharging port, a discharging device and a silo 1 for the flue gas inlet, a vertical cylinder 2 lined with heat-resistant or high-temperature-resistant materials, and a silo or discharging material at the bottom. The main body of the mechanism or cooling mechanism and blasting device and the outlet fan, flue, dust removal equipment, and material lifting or other transportation mechanisms are auxiliary equipment. The present invention is mainly an improvement to the vertical tube 2 . The vertical tube 2 includes an outer tube 3, an inner liner 4, two or more step plates 5 arranged in the inner cavity of the outer tube 3, close to the silo and directly to the bottom, separated by a certain distance, and staggered from each other, and between the step plates 5 More than two burners or other heat source inlets that are staggered from each other.
[0014] Each step plate 5 is arranged in...
PUM
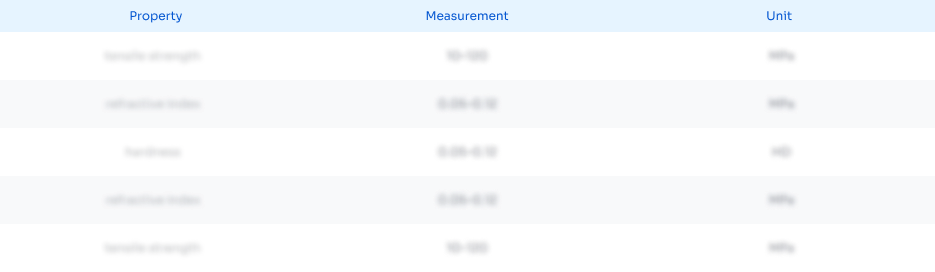
Abstract
Description
Claims
Application Information

- R&D
- Intellectual Property
- Life Sciences
- Materials
- Tech Scout
- Unparalleled Data Quality
- Higher Quality Content
- 60% Fewer Hallucinations
Browse by: Latest US Patents, China's latest patents, Technical Efficacy Thesaurus, Application Domain, Technology Topic, Popular Technical Reports.
© 2025 PatSnap. All rights reserved.Legal|Privacy policy|Modern Slavery Act Transparency Statement|Sitemap|About US| Contact US: help@patsnap.com