Golf head and connecting method of its surface plate
A golf head and panel technology, applied to golf balls, golf clubs, rackets, etc., can solve problems such as deformation, center of gravity displacement, heat source dispersion of welding bead, etc.
- Summary
- Abstract
- Description
- Claims
- Application Information
AI Technical Summary
Problems solved by technology
Method used
Image
Examples
Embodiment approach
[0027] see now figure 1 As shown, it is a schematic flow chart of the steps of the present invention. The present invention includes the manufacturing step 1 of manufacturing the batting panel and the ball head, the clamping and fixing step 2 of the batting surface processing, the freezing step 3 of freezing the panel, and the frozen rear panel. Step 4 of combining with the ball head, welding step 5 of welding the panel and the ball head, and step 6 of fixing the seat after cutting the ball head.
[0028] The manufacturing step 1 is to use the traditional precision machining method to manufacture the ball head and the panel first, the ball head is formed with a panel setting hole for setting the panel, and a screw thread is formed inside and extends outward relative to the other side of the panel setting hole. The fixing seat of the through hole communicating with the inside of the ball head, and the ball head is provided with a protrusion protruding toward the inside of the p...
PUM
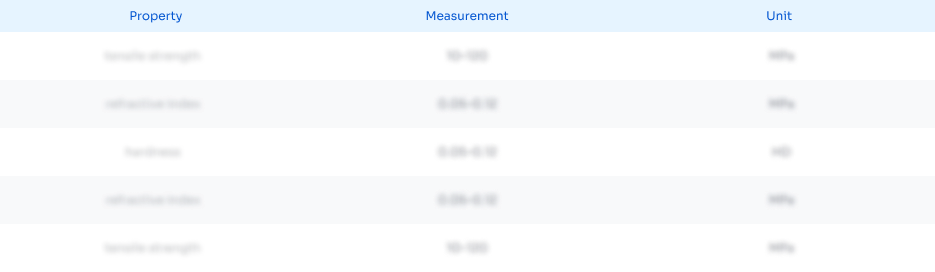
Abstract
Description
Claims
Application Information

- R&D
- Intellectual Property
- Life Sciences
- Materials
- Tech Scout
- Unparalleled Data Quality
- Higher Quality Content
- 60% Fewer Hallucinations
Browse by: Latest US Patents, China's latest patents, Technical Efficacy Thesaurus, Application Domain, Technology Topic, Popular Technical Reports.
© 2025 PatSnap. All rights reserved.Legal|Privacy policy|Modern Slavery Act Transparency Statement|Sitemap|About US| Contact US: help@patsnap.com