Process for preparing tertiary butanol
A technology of tert-butanol and isobutene, applied in the field of preparation of tert-butanol, can solve the problems of large weight ratio of tert-butanol, unavoidable butene polymerization problems, and high operating costs, so as to reduce production costs and eliminate butene polymerization side effects. reaction, the effect of improving the yield
- Summary
- Abstract
- Description
- Claims
- Application Information
AI Technical Summary
Problems solved by technology
Method used
Image
Examples
Embodiment 1
[0022] The production of tert-butanol is by-product mixed C4 in the steam cracking ethylene production process after removing butadiene as raw material, and the weight content of isobutene in C4 is 48.5%, and tetradecyl alcohol polyoxyethylene with a viscosity-average molecular weight of 300 is added to the water Ether, the add-on is 0.1% by weight, and the fixed-bed hydration reactor is filled with macroporous sulfonic acid ion exchange resins with an average particle size of Φ0.45mm, and the reaction section of the catalytic distillation tower is equipped with columnar sulfonic acid ion exchange resins. Exchange resin. Table 1 lists the operating conditions and results of the fixed bed reactor and catalytic distillation tower.
[0023] Table 1 The test results of C4 synthesis of tert-butanol by-product of ethylene cracking unit
[0024] project result
[0025] fixed bed reactor
[0026] C4 liquid phase velocity, h -1 0.45
[00...
Embodiment 2
[0051] The C4 distillate produced by catalytic cracking in an oil refinery is used as a raw material to produce tert-butanol. The isobutene content in C4 is 21.8% by weight, and nonylphenol polyoxyethylene ether with a molecular weight of 650 is added to water in an amount of 0.06% by weight. The reactor is filled with macroporous sulfonic acid ion exchange resin with a particle size of Φ0.45mm, and the reaction section of the catalytic distillation tower is filled with Raschig ring-shaped sulfonic acid ion exchange resin. Table 2 lists the operating conditions and results of the fixed bed reactor and catalytic distillation tower.
[0052] Table 2 Test results of FCC synthesis of tert-butanol
[0053] project result
[0054] fixed bed reactor
[0055] C4 liquid phase velocity, h -1 0.35
[0056] Water / carbon four, v / v 1:1
[0057] Inlet temperature, ℃ 60
[0058] Pressure, MPa 1.5
[0059] Tert-butanol selectivity, % 99.8...
PUM
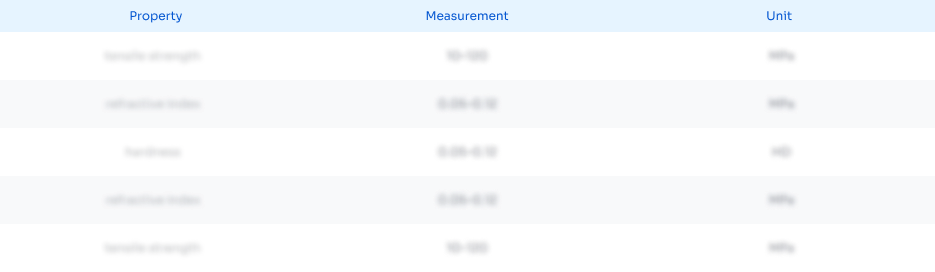
Abstract
Description
Claims
Application Information

- R&D Engineer
- R&D Manager
- IP Professional
- Industry Leading Data Capabilities
- Powerful AI technology
- Patent DNA Extraction
Browse by: Latest US Patents, China's latest patents, Technical Efficacy Thesaurus, Application Domain, Technology Topic, Popular Technical Reports.
© 2024 PatSnap. All rights reserved.Legal|Privacy policy|Modern Slavery Act Transparency Statement|Sitemap|About US| Contact US: help@patsnap.com