Production method of foaming type wood plastic recombination wood
A production method and technology for reconstituting wood, applied in the field of manufacturing plastic-wood profiles, can solve the problems that profiles cannot be used as stress-bearing structural parts, the proportion cannot be too high, and the stress strength is weakened, etc. The effect of increased affinity and increased plastic surface area
- Summary
- Abstract
- Description
- Claims
- Application Information
AI Technical Summary
Problems solved by technology
Method used
Examples
Embodiment 1
[0016] Polyolefin waste plastics (microcellular foaming - low foaming rate: 2-3) 1 part (weight ratio)
[0017] 6 parts (by weight) of dried plant stem sheet through rolling
[0018] (Poplar; Thickness: 0.8mm-1.5mm; 5.6% moisture content)
[0019] Oriented pavement assembly;
[0020] Pressure: 4.6Mpa;
[0021] Foaming temperature: 160℃~230℃;
[0022] Hot open the mold.
[0023] The performance indexes of the obtained foamed recombined wood are shown in Table 1.
[0024] Project Unit
value
Plate thickness MM
10
Density KG / M 3
0.44
Plane tensile strength MPa
1.53
Screw holding force on vertical board surface N
1812
Longitudinal static bending strength MPa
77.3
Transverse static bending strength MPa
44.6
Longitudinal elastic modulus MPa
5132
Transverse elastic modulus MPa
3363
Surface resistance value Ω
2.3×10 11
Breakd...
PUM
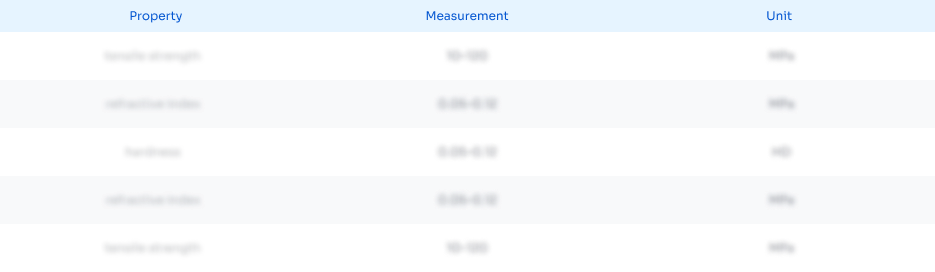
Abstract
Description
Claims
Application Information

- Generate Ideas
- Intellectual Property
- Life Sciences
- Materials
- Tech Scout
- Unparalleled Data Quality
- Higher Quality Content
- 60% Fewer Hallucinations
Browse by: Latest US Patents, China's latest patents, Technical Efficacy Thesaurus, Application Domain, Technology Topic, Popular Technical Reports.
© 2025 PatSnap. All rights reserved.Legal|Privacy policy|Modern Slavery Act Transparency Statement|Sitemap|About US| Contact US: help@patsnap.com