Method for separating magma in producing soda process
A technology of production process and crystalline slurry, which is applied in the direction of carbonate preparation, etc., can solve the problems of low production efficiency of the alkali filter, increase the load of the alkali filter, and large washing water of the alkali filter, and achieve a small footprint, The effect of low maintenance rate and simple equipment
- Summary
- Abstract
- Description
- Claims
- Application Information
AI Technical Summary
Problems solved by technology
Method used
Examples
Embodiment 1
[0012] Example 1. A method for separating crystal slurry in the production process of soda ash. After sodium bicarbonate crystallization is synthesized in a carbonization tower, the crystal slurry is taken out from the carbonization tower and introduced into a hydrocyclone for hydrocyclone separation. When the hydrocyclone After the solid-to-liquid ratio of the internal crystal slurry reaches 35%, the crystal slurry is introduced into an alkali filter for separation, and the solid obtained after separation is calcined to obtain soda ash.
Embodiment 2
[0013] Example 2. A method for separating crystal slurry in the production process of soda ash. After sodium bicarbonate crystallization is synthesized in a carbonization tower, the crystal slurry is taken out from the carbonization tower and introduced into a hydrocyclone for hydrocyclone separation. When the hydrocyclone After the solid-liquid ratio of the inner crystal slurry reaches 40%, the crystal slurry is introduced into the alkali filter for separation, and the overflow mother liquor exported from the overflow port of the liquid cyclone separator enters the soda production system for recycling, and the solid obtained after separation is recycled. Calcined to obtain soda ash.
Embodiment 3
[0014] Example 3. A method for separating crystal slurry in the production process of soda ash. After sodium bicarbonate crystallization is synthesized in a carbonization tower, the crystal slurry is taken out from the carbonization tower and introduced into a hydrocyclone for hydrocyclone separation. When the hydrocyclone After the solid-to-liquid ratio of the internal crystalline slurry reaches 38%, the crystalline slurry is introduced into an alkali filter for separation, and the solid obtained after separation is calcined to obtain soda ash.
PUM
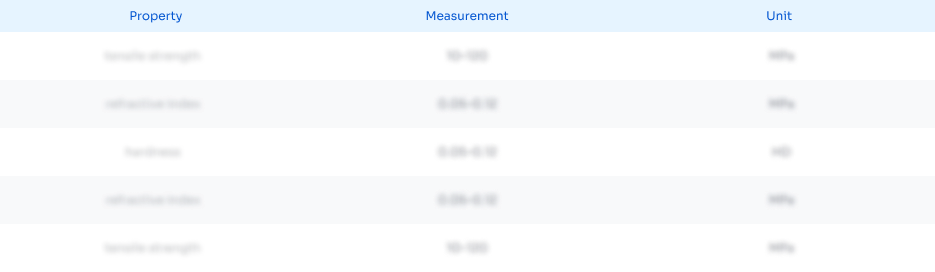
Abstract
Description
Claims
Application Information

- Generate Ideas
- Intellectual Property
- Life Sciences
- Materials
- Tech Scout
- Unparalleled Data Quality
- Higher Quality Content
- 60% Fewer Hallucinations
Browse by: Latest US Patents, China's latest patents, Technical Efficacy Thesaurus, Application Domain, Technology Topic, Popular Technical Reports.
© 2025 PatSnap. All rights reserved.Legal|Privacy policy|Modern Slavery Act Transparency Statement|Sitemap|About US| Contact US: help@patsnap.com