Electronic emitting element, electronic source, image displaying device, and their mfg. method
A technology of electron emission and manufacturing method, which is applied in the manufacture of discharge tubes/lamps, electrical components, electrode systems, etc. It can solve the problems of uniformity reduction, complicated process management, and difficulty in forming film thickness with high precision.
- Summary
- Abstract
- Description
- Claims
- Application Information
AI Technical Summary
Problems solved by technology
Method used
Image
Examples
Embodiment 1
[0335] This example is an example of manufacturing the electron-emitting element of the present invention shown in FIG. 1 .
[0336] Since the following laser beams can pass through the substrate by using a glass substrate as the substrate 1 , laser irradiation can be performed regardless of the front and back of the glass substrate. As a material of the opposing electrodes 2 and 3, platinum which has high heat resistance against the following laser irradiation and especially high thermal conductivity is used. As the polymer film 4, aromatic polyimide is used.
[0337] Hereinafter, the method of manufacturing the electron emission element of this embodiment will be described using FIG. 1, FIG. 2, and FIG. 3. FIG.
[0338] (Process 1)
[0339] Use quartz glass as the substrate 1, clean the substrate 1 sufficiently with detergent, pure water, organic solvent, etc. Electrodes 2, 3 are formed thereon (FIG. 2(a)). At this time, the electrode interval L was set to 10 μm, the wid...
Embodiment 2
[0355] In this example, basically, an electron emission element was produced by the same process as in Example 1, but in this example, electron beam irradiation was used for the low-resistance treatment. Therefore, here, the steps after the step 3 of the first embodiment will be described using FIG. 8 .
[0356] (Process 3)
[0357] Place the substrate 1 formed with the electrodes 2, 3 and the polymer film 4 in a vacuum container equipped with an electron gun. After sufficient exhaust, the irradiation position of the center of the electron beam comes to the electrode 3, and on the electrode 3 Electron beams are irradiated (see Fig. 8(a), (b)). The irradiation condition of the electron beam at this time was set so that the accelerating voltage Vac=10 kV. The spot diameter of the electron beam is set at about 200 μm, and the center thereof is set at a distance of 100 μm or more upward from the end of the electrode 3, and the electron beam is directly irradiated between the ele...
Embodiment 3
[0367] The electron emission element of this embodiment is basically the same form as the electron emission element of the above-mentioned embodiment, but the manufacturing method is partially different.
[0368] First, electrodes 2 and 3 and a polymer film 4 made of a polyimide film were fabricated on a substrate 1 made of quartz glass in the same manner as Steps 1 and 2 of Example 1. The electrode interval L was wider than the previous embodiment and was set to 20 µm, the width W of the electrodes was set to 500 µm, and the thickness thereof was set to 100 nm. In addition, the width W' of the polymer film 4 was set to 300 µm.
[0369] When the electrode interval L is wide, as shown in Example 1 or Example 2, in the process of reducing the resistance of the polymer film 4 caused by electrode heating and heat conduction, the electrical resistance of the polymer film 4 cannot be sufficiently changed. The case of conduction characteristics.
[0370] Therefore, the process of u...
PUM
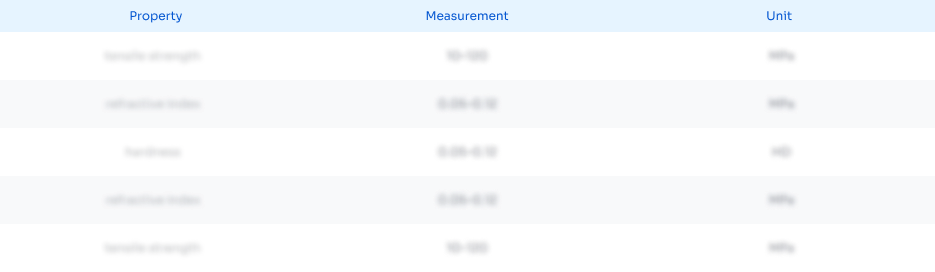
Abstract
Description
Claims
Application Information

- R&D Engineer
- R&D Manager
- IP Professional
- Industry Leading Data Capabilities
- Powerful AI technology
- Patent DNA Extraction
Browse by: Latest US Patents, China's latest patents, Technical Efficacy Thesaurus, Application Domain, Technology Topic, Popular Technical Reports.
© 2024 PatSnap. All rights reserved.Legal|Privacy policy|Modern Slavery Act Transparency Statement|Sitemap|About US| Contact US: help@patsnap.com