Double-metal exhaust gate for diesel engine of diesel locomotive and its manufacture
A diesel locomotive and bimetal technology, applied in the field of exhaust valves, can solve the problems that the performance cannot meet the working requirements, affect the structural performance of the valve, and the service life cannot be satisfied, etc. Effect
- Summary
- Abstract
- Description
- Claims
- Application Information
AI Technical Summary
Problems solved by technology
Method used
Image
Examples
Embodiment 1
[0033] The manufacturing material of the diesel locomotive diesel bimetal exhaust valve of the present invention is a super-iron-nickel alloy, and its chemical composition specification (wt%) typical composition can be selected as: C: 0.05; Si: 0.15 / 0.20; Mn: 0.60 / 0.70; Cr: 20.0 / 21.0; Ni: 38.0 / 40.0; Ti: 2.70 / 2.90; AI: 0.90 / 1.10; Nb: 0.60 / 0.80; V; 0.02 / 0.08; W: 0.60 / 0.70; 0.02; Ce: 0.005 / 0.01; Co: 0.50 / 0.70; Mo: 0.15 / 0.20; Cu: 0.05 / 0.15;
Embodiment 2
[0035] The manufacturing material of the diesel bimetallic exhaust valve for diesel locomotive of the present invention is a super-iron-nickel alloy, and its chemical composition specification (wt%) typical composition can be selected as: C: 0.08; Si: 0.25 / 0.40; Mn: 0.65 / 0.75; Cr: 21.0 / 22.0; Ni: 36.0 / 38.0; Ti: 2.60 / 2.80; AI: 0.85 / 1.0; Nb: 0.70 / 0.85; V: 0.10-0.15; W: 0.70 / 0.80; 0.02; Ce: 0.02 / 0.04; Co: 0.7 / 0.8; Mo: 0.20 / 0.25; Cu: 0.10 / 0.20;
Embodiment 3
[0037]The manufacturing material of the diesel locomotive diesel bimetal exhaust valve of the present invention is a super-iron-nickel alloy, and its chemical composition specification (wt%) typical composition can be selected as: C: 0.15; Si: 0.35 / 0.55; Mn: 0.70 / 0.80; Cr: 22.0 / 23.0; Ni: 31.0 / 34.0; Ti: 2.50 / 2.60; AI: 0.65 / 0.80; Nb: 0.80 / 0.95; V: 0.15-0.20; W: 0.80 / 0.90; 0.02; Ce: 0.05 / 0.07; Co: 0.80 / 0.95; Mo: 0.25 / 0.30; Cu: 0.20 / 0.25;
[0038] Under the chemical composition ratio of any of the above-mentioned embodiments, the manufacturing method of diesel bimetallic exhaust valve for diesel locomotive is: material preparation→valve blank forming→heat treatment→machining→surface strengthening treatment
[0039] 1. Material preparation: The material of the valve disc is super-iron-nickel alloy polished bar, which is cut to a fixed length, and the deformed end is made with a specific R; the material of the valve stem is polished bar of low alloy structural steel.
[0040] 2. El...
PUM
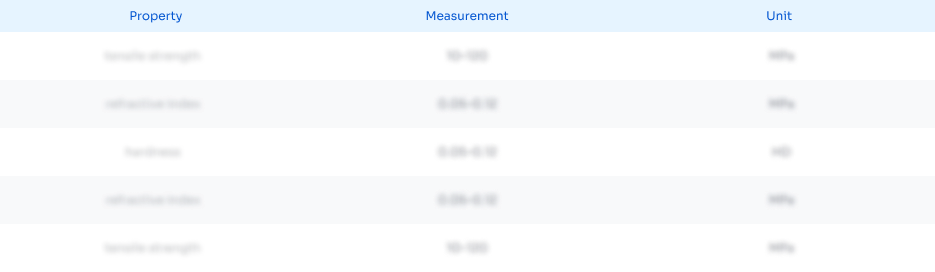
Abstract
Description
Claims
Application Information

- R&D
- Intellectual Property
- Life Sciences
- Materials
- Tech Scout
- Unparalleled Data Quality
- Higher Quality Content
- 60% Fewer Hallucinations
Browse by: Latest US Patents, China's latest patents, Technical Efficacy Thesaurus, Application Domain, Technology Topic, Popular Technical Reports.
© 2025 PatSnap. All rights reserved.Legal|Privacy policy|Modern Slavery Act Transparency Statement|Sitemap|About US| Contact US: help@patsnap.com