Preparation method of affinity polysulfone-chitosan compound asymmetrical ultrafiltration film
A technology of chitosan and ultrafiltration membranes, applied in chemical instruments and methods, membrane technology, semipermeable membrane separation, etc., can solve problems such as complex activation methods, single active groups, and no consideration of the internal structure of the membrane, and achieve Ideal pore structure, simple preparation method, and good mechanical strength
- Summary
- Abstract
- Description
- Claims
- Application Information
AI Technical Summary
Problems solved by technology
Method used
Image
Examples
Example Embodiment
[0011] Example 1: 1. Preparation of chloromethylated polysulfone asymmetric membrane
[0012] Take the chloromethylated polysulfone and polyethylene glycol and place them in dimethylformamide, the chloromethylated polysulfone / polyethylene glycol is 4 / 1, the molecular weight of polyethylene glycol is 600, 80-85℃ Stir for 12 hours. Then put the casting solution in a dark place and stand for 24 hours. Pour the casting liquid on the glass plate, the temperature of the glass plate is 50 ℃, scrape with a spatula to form a film, evaporate for 30 seconds, immerse in distilled water, and solidify for 1 hour. The solidified membrane was taken out and rinsed with running water for 24 hours to obtain a chloromethylated polysulfone asymmetric membrane with through holes at the bottom. 2. Preparation of hydroxymethyl polysulfone membrane
[0013] Take the chloromethylated polysulfone membrane prepared in step 1 and place it in a 15% soda ash solution and shake at a constant temperature of 85° C...
Example Embodiment
[0015] Embodiment two:
[0016] Take the chloromethylated polysulfone and ethylene glycol monomethyl ether and place them in N-methylpyrrolidone, the chloromethylated polysulfone / ethylene glycol monomethyl ether is 4 / 1, and stir at 80-85°C for 15 hours. Then put the casting solution in a dark place and stand for 24 hours. Pour the casting liquid on the glass plate, the temperature of the glass plate is 70 ℃, scrape with a scraper to form a film, evaporate for 1 minute, immerse in a 10% propionic acid solution, and solidify for 1 hour. The solidified film was taken out and rinsed with running water for 24 hours. The chloromethylated polysulfone asymmetric membrane is obtained.
[0017] The hydroxymethyl polysulfone membrane and polysulfone-chitosan composite membrane were prepared according to the scheme of Example 1.
Example Embodiment
[0018] Embodiment three:
[0019] Dissolve 80 mg of sodium borohydride in 12 ml of 2M NaOH, add 20 ml of water and 4 ml of dioxirane. The methylol polysulfone membrane prepared in Example 1 was placed in the above solution, shaken and activated at room temperature for 4 hours, and then washed with distilled water 3 times. The activated membrane was placed in a 2% chitosan acetic acid solution with an acetic acid concentration of 10% (volume), shaken at 40°C for 5 hours, and then placed in an oven at 120°C to dry for 4 hours. The dried membrane was washed with 1% acetic acid solution for 1 hour, and washed with a large amount of distilled water for 1 day to obtain a polysulfone-chitosan composite membrane.
PUM
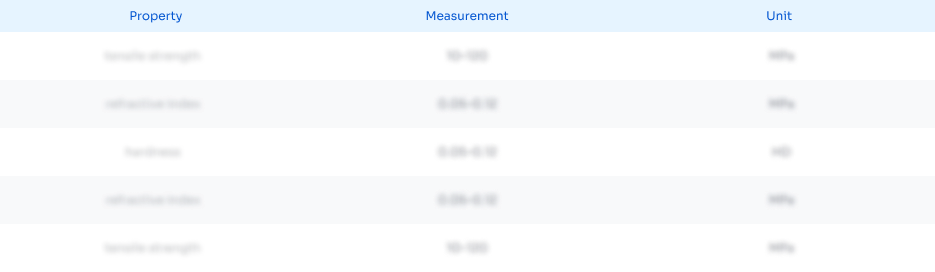
Abstract
Description
Claims
Application Information

- R&D
- Intellectual Property
- Life Sciences
- Materials
- Tech Scout
- Unparalleled Data Quality
- Higher Quality Content
- 60% Fewer Hallucinations
Browse by: Latest US Patents, China's latest patents, Technical Efficacy Thesaurus, Application Domain, Technology Topic, Popular Technical Reports.
© 2025 PatSnap. All rights reserved.Legal|Privacy policy|Modern Slavery Act Transparency Statement|Sitemap|About US| Contact US: help@patsnap.com