Manufacture of directional electromagnetic steel plate
A technology of electromagnetic steel sheet and manufacturing method, which is applied in the field of manufacturing oriented electrical steel sheet, and can solve the problems of low magnetic flux density and the like
- Summary
- Abstract
- Description
- Claims
- Application Information
AI Technical Summary
Problems solved by technology
Method used
Image
Examples
Embodiment 1
[0138] Continuous casting produced steel sheets with material compositions shown in Table 1. All components not shown in Table 1 were reduced to 50 ppm or less. These sheets were formed into 2.2 mm thick hot-rolled sheets by heating the sheets at 1030 degrees for 20 minutes followed by hot rolling. After performing soaking annealing at 1000 degrees Celsius for 30 seconds, the final plate thickness of 0.30 mm was completed by cold rolling at normal temperature.
[0139] Primary recrystallization annealing was performed by soaking at 930° C. for 10 seconds in an atmosphere of hydrogen: 25 vol %, nitrogen: 75 vol %, and dew point: −30° C. After that, without using an annealing separator, in a mixed atmosphere of nitrogen: 50vol%, argon: 50vol% (dew point: -30 degrees) at a rate of 50 degrees / h to 800 degrees, above 800 degrees at 10 degrees / h The speed is heated to 880 degrees, and kept at this temperature for 50 hours for secondary recrystallization annealing (annealing is...
Embodiment 2
[0148] After heating the steel plate with the material composition shown in Table 2 to 1125 degrees, it was hot-rolled to form a 2.8 mm thick hot-rolled plate. All components not shown in Table 2 were reduced to 50 ppm or less.
[0149] These cold-rolled sheets were subjected to hot-rolled sheet annealing at 1000° C. for 60 seconds, and cold-rolled to obtain a final sheet thickness of 0.30 mm. Primary recrystallization annealing was performed by soaking at 920° C. for 20 seconds in an atmosphere of hydrogen: 50 vol %, nitrogen: 50 vol %, and dew point: −50° C. After that, without using an annealing separator, the temperature was raised to 900°C at a rate of 10°C / h, and the secondary recrystallization annealing at 900°C for 75 hours was carried out in a nitrogen atmosphere with a dew point of -40°C (annealing was finally completed).
[0150] After the secondary recrystallization annealing, a tension of 4Mpa is applied to the steel plate, and a flattening annealing at 875°C for...
Embodiment 3
[0158] Continuous casting manufacturing contains C: 0.030%, Si: 3.3%, Mn: 0.05%, and Sb: 0.02%, and Al is reduced to 40ppm, N is reduced to 20ppm, all other components are reduced to less than 50ppm, and the rest is Fe and unavoidable A steel plate composed of impurities. After heating the plate at 1100°C for 30 minutes, a hot-rolled plate with a thickness of 3.2 mm was formed by hot rolling, and the hot-rolled plate was annealed under the conditions shown in Table 3. Thereafter, the final sheet thickness of 0.50 mm was completed by cold rolling at a temperature of 250°C.
[0159]Primary recrystallization annealing with soaking for 30 seconds was performed at 900° C. in a mixed atmosphere of 30° C. dew point, 75 vol % nitrogen, and 25 vol % hydrogen. Afterwards, using forsterite as an annealing separator, in a nitrogen atmosphere with a dew point of -20°C, the temperature was raised to 1000°C at a rate of 50°C / h for final annealing.
[0160] After secondary recrystallization...
PUM
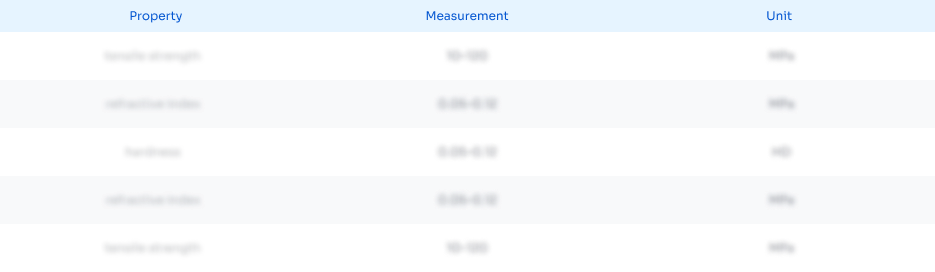
Abstract
Description
Claims
Application Information

- R&D
- Intellectual Property
- Life Sciences
- Materials
- Tech Scout
- Unparalleled Data Quality
- Higher Quality Content
- 60% Fewer Hallucinations
Browse by: Latest US Patents, China's latest patents, Technical Efficacy Thesaurus, Application Domain, Technology Topic, Popular Technical Reports.
© 2025 PatSnap. All rights reserved.Legal|Privacy policy|Modern Slavery Act Transparency Statement|Sitemap|About US| Contact US: help@patsnap.com