Combined multi-stage filter core and its making method
A technology of filter element and composite layer, which is applied in the field of composite multi-stage filter element and its manufacture, can solve the problems of filter element clogging, low filtration precision, short service life, etc., and achieve the effect of improved removal rate, high filtration precision and long service life
- Summary
- Abstract
- Description
- Claims
- Application Information
AI Technical Summary
Problems solved by technology
Method used
Examples
Embodiment 1
[0046] Embodiment 1: make the filter element of the present invention with composite material A, wherein composite material A is prepared by the following method:
[0047] (1) Crush the peanut shells to 5-50 mesh with a rotary cutter, sieve and sort according to 5-10 mesh, 10-30 mesh, and 30-50 mesh, and then soak them in 3% p-toluenesulfonic acid for 5 hours , it is advisable to completely immerse the peanut shells in the acid solution, remove them separately, and add 1% hydrogen peroxide and 1% tannin respectively, mix and set aside;
[0048] (2) Dry the leftover cottonseed husks produced by the oil factory, remove part of the remaining cottonseed kernels, sieve and sort by 10-30 mesh and 30-50 mesh, soak them in 8% sodium hydroxide lye for 15 minutes hours, it is advisable to completely immerse the cottonseed shells with the lye, and then fish them out for subsequent use;
[0049] (3) Cut and crush banana leaves, coconut leaves, coconut peel, asparagus, scutellaria, mat gr...
Embodiment 2
[0059] Embodiment 2: This embodiment uses the A-type material, and the processing method of the composite material A and the manufacturing method of the filter element are the same as in Embodiment 1, except that the concentration of the acid and lye and the ratio of the materials are used.
[0060] Wherein, (1) was soaked with 7% hydrochloric acid for 2 hours; (2) was soaked with 3% sodium hydroxide lye for 20 hours; (3) was soaked with 2% liquid alkali for 2 hours; (4) was soaked with Soak in 5% liquid alkali for 15 hours;
[0061] The raw materials are mixed and stirred according to the following parts by weight to form 5-10 mesh material, 10-30 mesh material and 30-50 mesh material respectively:
[0062] Peanut shells: 70 kg; Cottonseed shells: 5 kg; Coconut leaves: 5 kg;
[0063] Coconut shell: 50 kg; Alumina: 3 kg; Silica gel: 1 kg; Activated carbon:
Embodiment 3
[0065] Embodiment 3: This embodiment uses A-type material, and the processing method of composite type material A and the manufacture method of filter core are identical with embodiment 1, 2, and difference is the use ratio of the concentration of use acid, lye and material.
[0066] Wherein, (1) was soaked with 5% hydrochloric acid for 3 hours; (2) was soaked with 5% sodium hydroxide lye for 18 hours; (3) was soaked with 2% liquid alkali for 3 hours; (4) was soaked with Soak in 5% liquid alkali for 18 hours;
[0067] The raw materials are mixed and stirred according to the following parts by weight to form 5-10 mesh material, 10-30 mesh material and 30-50 mesh material respectively:
[0068] 64 kg of peanut shells; 14 kg of cottonseed shells; 4 kg of coconut leaves;
[0069] 13 kg of coconut shell; 1 kg of alumina; 1 kg of silica gel; 3 kg of activated carbon;
[0070] 1 kg of 6% sodium hydroxide solution.
PUM
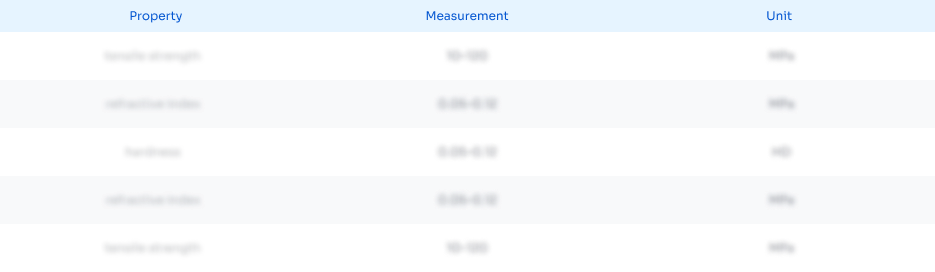
Abstract
Description
Claims
Application Information

- Generate Ideas
- Intellectual Property
- Life Sciences
- Materials
- Tech Scout
- Unparalleled Data Quality
- Higher Quality Content
- 60% Fewer Hallucinations
Browse by: Latest US Patents, China's latest patents, Technical Efficacy Thesaurus, Application Domain, Technology Topic, Popular Technical Reports.
© 2025 PatSnap. All rights reserved.Legal|Privacy policy|Modern Slavery Act Transparency Statement|Sitemap|About US| Contact US: help@patsnap.com