Chlorination and resin method for shrink-resist treatment of knitting wool
A technology of shrink-proof treatment and chlorination treatment, which is applied in fiber treatment, textile and paper making, etc., to achieve the effect of improving intrinsic quality and wearability and maintaining inherent characteristics
- Summary
- Abstract
- Description
- Claims
- Application Information
AI Technical Summary
Problems solved by technology
Method used
Examples
Embodiment 1
[0019] Variety 214 / 4 pure capillary wool 200 kg, color number 2225 maroon, equipment: jet dyeing machine made in Japan.
[0020] The two processes of chlorination treatment and resin treatment are completed by the following steps: (wherein the percentage is calculated by the weight of plush yarn)
[0021] (1) Wash with water at 40°C for 10 minutes;
[0022] (2) Treat in 14 kg of sodium dichloroisocyanurate liquid for 20 minutes;
[0023] (3) Put in 14 kg of sodium bisulfite and keep it at a temperature of 55°C for 30 minutes;
[0024] (4) Change the water;
[0025] (5) Dyeing;
[0026] (6) Put in 12 kg of silicone resin and keep the water temperature at 40°C for treatment
[0027] 40 minutes;
[0028] (7) Dehydration and drying.
[0029] After the shrink-proof treatment is completed, the shrink-resistant processed product is obtained.
Embodiment 2
[0031] Variety 214 / 4 pure capillary yarn 100 kg, color number 2225 maroon, equipment: jet dyeing machine made in Japan.
[0032] The two processes of chlorination treatment and resin treatment are completed by the following steps: (wherein the percentage is calculated by the weight of plush yarn)
[0033] (1) Wash with water at 40°C for 10 minutes;
[0034] (2) Treat in 7 kg of sodium dichloroisocyanurate liquid for 18 minutes;
[0035] (3) Add 7 kg of sodium bisulfite and keep it at a temperature of 55°C for 30 minutes;
[0036] (4) Change the water;
[0037] (5) Dyeing;
[0038] (6) Put 6 kg of silicone resin, and keep the water temperature at 40°C for 40
[0039] minute;
[0040] (7) Dehydration and drying.
[0041] After the shrink-proof treatment is completed, the shrink-resistant processed product is obtained.
[0042] Wool products are subjected to this anti-shrinkage treatment to maintain the characteristics of the original wool fiber, and the anti-shrinkage eff...
PUM
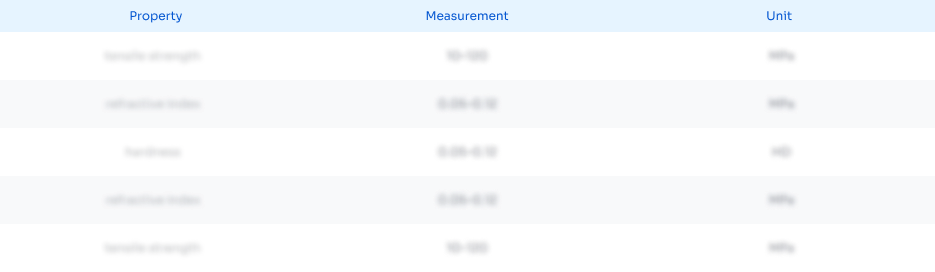
Abstract
Description
Claims
Application Information

- R&D Engineer
- R&D Manager
- IP Professional
- Industry Leading Data Capabilities
- Powerful AI technology
- Patent DNA Extraction
Browse by: Latest US Patents, China's latest patents, Technical Efficacy Thesaurus, Application Domain, Technology Topic, Popular Technical Reports.
© 2024 PatSnap. All rights reserved.Legal|Privacy policy|Modern Slavery Act Transparency Statement|Sitemap|About US| Contact US: help@patsnap.com