Process for extracting nickel from nickel sulfide material with low copper content
A technology of nickel sulfide and materials, which is applied in the field of extracting nickel from nickel sulfide materials with low copper content, can solve the problems of complex metal recovery process and high cost, and achieve the effect of simple leaching process route, low cost and high direct metal recovery rate
- Summary
- Abstract
- Description
- Claims
- Application Information
AI Technical Summary
Problems solved by technology
Method used
Image
Examples
example 1
[0033] Composition (%) of the leached nickel concentrate used: Ni 66.27, Cu 2.65, Fe 2.32, Co0,85, S 23.75.
[0034] The pressure leaching conditions are as follows: take 100g of nickel concentrate, add 18g of sulfur, the leaching liquid-solid ratio is 6:1, the leaching temperature is 140°C, the oxygen partial pressure is 150kPa, and the reaction time is 3 hours.
[0035] Leaching rate (%)
example 2
[0037] Composition (%) of the leached nickel concentrate used: Ni 66.27, Cu 2.65, Fe 2.32, Co0,85, S 23.75.
[0038] The pressure leaching conditions are as follows: take 100g of nickel concentrate, add 26ml of concentrated sulfuric acid, the leaching liquid-solid ratio is 5:1, the leaching temperature is 145°C, the oxygen partial pressure is 200kPa, and the reaction time is 3.5 hours.
[0039] Leaching rate (%)
example 3
[0041] Composition (%) of the leached nickel concentrate used: Ni 66.27, Cu 2.65, Fe 2.32, Co0,85, S 23.75.
[0042] Leaching rate (%)
PUM
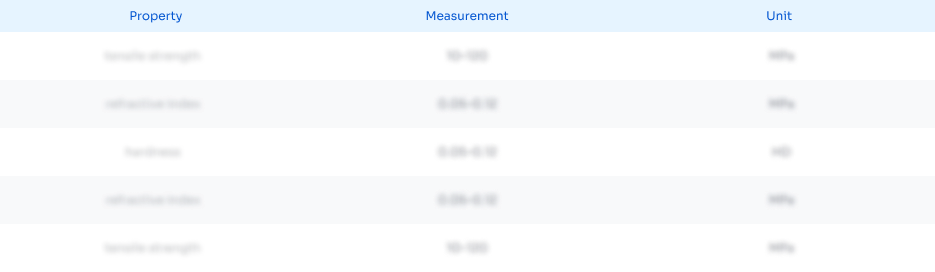
Abstract
Description
Claims
Application Information

- R&D Engineer
- R&D Manager
- IP Professional
- Industry Leading Data Capabilities
- Powerful AI technology
- Patent DNA Extraction
Browse by: Latest US Patents, China's latest patents, Technical Efficacy Thesaurus, Application Domain, Technology Topic, Popular Technical Reports.
© 2024 PatSnap. All rights reserved.Legal|Privacy policy|Modern Slavery Act Transparency Statement|Sitemap|About US| Contact US: help@patsnap.com