Polyamide resin compsns.
A technology of polyamide resin and composition, which is applied in the field of polyamide resin composition and its molded products, and can solve the problems of poor compatibility between semi-aromatic polyamide and polybrominated styrene, poor chemical resistance, surface peeling, etc.
- Summary
- Abstract
- Description
- Claims
- Application Information
AI Technical Summary
Problems solved by technology
Method used
Image
Examples
Embodiment 1-5
[0057] The above-mentioned polyamide resin was mixed with polybromostyrene (hereinafter referred to as "GMA-PBrS") containing 2.0 mol% glycidyl methacrylate, polybromostyrene (PBS-64 of Great Lakes Chemical, hereinafter referred to as "PBrS"), zinc borate (Borax's Fire Break 415), a mixture of sodium oxide and antimony pentoxide (Nissan Chemical's Sun-EpocNA-1070L), zinc stannate (Nippon Light Metal's FLAMTARD-S), and glass fiber (Nitto Boseki's CS-3J-256S) was premixed in the proportions shown in Table 1 below. The resulting mixture was fed into a twin-screw extruder (TEX44C by Nippon Seikosho), kneaded and extruded in a molten state at a barrel temperature of 320° C., then cooled and cut into pelletized polyamide resin compositions. The pellets were molded in an injection molding machine (barrel temperature 330°C, molding temperature 150°C), and the resulting molded articles were examined as described above. The test results are shown in Table 1. Comparative example 1-2
PUM
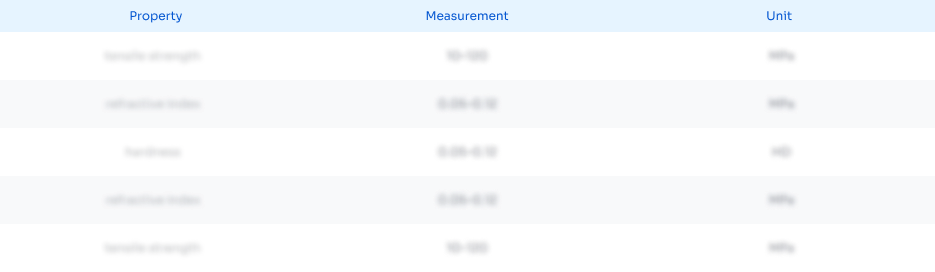
Abstract
Description
Claims
Application Information

- R&D
- Intellectual Property
- Life Sciences
- Materials
- Tech Scout
- Unparalleled Data Quality
- Higher Quality Content
- 60% Fewer Hallucinations
Browse by: Latest US Patents, China's latest patents, Technical Efficacy Thesaurus, Application Domain, Technology Topic, Popular Technical Reports.
© 2025 PatSnap. All rights reserved.Legal|Privacy policy|Modern Slavery Act Transparency Statement|Sitemap|About US| Contact US: help@patsnap.com