Grinding drum and stirring mill of grinding and crushing machinery
A grinding drum and mechanical technology, applied in the field of grinding drums and stirring mills, can solve the problem of inability to precisely control particle size distribution, etc., and achieve the effect of improving grinding efficiency
- Summary
- Abstract
- Description
- Claims
- Application Information
AI Technical Summary
Problems solved by technology
Method used
Image
Examples
Embodiment 1
[0020] Example 1. A grinding cylinder of a grinding and pulverizing machine. With reference to Figures 1 to 4, the cylinder is cylindrical, and a discharge port 1 is provided near the center of the end surface at one end of the cylinder. The cylinder includes three parts with different structures, which are far away from A section of the discharge port 1 is the rotating speed section 2. This section has such a structure that the cross section of the inner wall is a regular hexagon, the longitudinal section is a trapezoid, and the side 5 close to the discharge port 1 is the long base; The inner wall is cylindrical; the part 4 located at the end of the discharge port has such a structure, the cross section of the inner wall is circular, the longitudinal section is trapezoidal, and the side 6 close to the discharge port 1 is the long bottom side.
[0021] In the above-mentioned embodiment, the cross-sectional profile of the inner wall of the rotating transmission section 2 may also b...
Embodiment 2
[0022] The second embodiment, an agitating mill, combined with Fig. 7, includes a grinding drum 7, a transmission mechanism 8 and a rotating spindle 9. The grinding drum has the structure in the first embodiment, and the feed port 10 is arranged opposite to the discharge port. At one end, the rotating main shaft 8 is arranged in the cylinder axially, and the transmission mechanism 8 drives the rotating main shaft 9 to rotate.
[0023] The specific working process: add water to the material to make a slurry with a solid content of 70%-75%, and use a pump (not shown) to send it to the inlet 10 at the bottom of the barrel. The inside of the mill barrel is driven by the rotating spindle 9 to drive the disc (not shown). Draw) High-speed rotation (1200-3000 rpm) produces strong centrifugal shearing force and squeezing collision force. The slurry rises from the bottom of the cylinder to the top discharge port 1 under a certain pressure.
[0024] When the material is in the lower part 2 o...
PUM
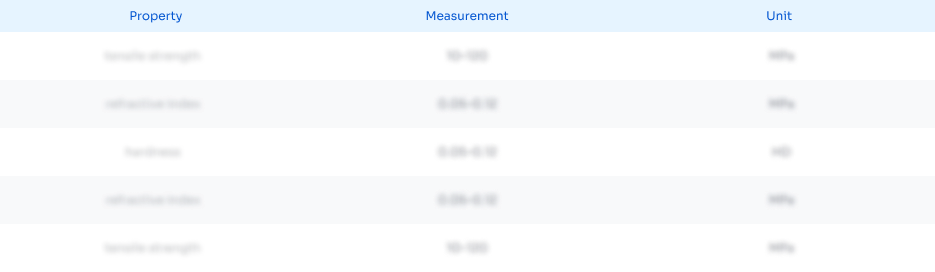
Abstract
Description
Claims
Application Information

- R&D Engineer
- R&D Manager
- IP Professional
- Industry Leading Data Capabilities
- Powerful AI technology
- Patent DNA Extraction
Browse by: Latest US Patents, China's latest patents, Technical Efficacy Thesaurus, Application Domain, Technology Topic, Popular Technical Reports.
© 2024 PatSnap. All rights reserved.Legal|Privacy policy|Modern Slavery Act Transparency Statement|Sitemap|About US| Contact US: help@patsnap.com