High temperature luminous glazing and its production process and application in luminous glazed tile
A processing technology, luminous glaze technology, applied in the production of luminous glaze, the application field of production of luminous tiles, can solve the problems of human body and environmental damage, poor stability, luminous pigment easy to lose light, etc., achieve short light absorption time, strong active effect
- Summary
- Abstract
- Description
- Claims
- Application Information
AI Technical Summary
Problems solved by technology
Method used
Examples
Embodiment 1
[0024] Example 1 The luminous parameters are measured according to DIN67510, and the brightness at the 10th minute is 202.9mcd / m 2
[0025] 1. The high-temperature luminescent glaze is composed of the following components by weight percentage:
[0026] SrAl 2 o 4 EuDy (alkaline earth aluminate) 50%, SiO 2 40%, Al 2 o 3 6%, CaO2.5%, MgO 1.0%, Fe2O3 0.5%;
[0027] 2. The processing technology of the above-mentioned high-temperature luminescent glaze includes the following contents:
[0028] A. Mix and grind
[0029] After mixing the components described in 1 above, place them in a ball mill for 6 hours; and sieve to 325 mesh;
[0030] B. High temperature melting
[0031] Put the mixed and ground luminescent glaze on the shuttle furnace of the oxidation isolation device to burn the frit, the firing temperature is 800-1000°C, and the firing time is 3-6 hours;
[0032] C. Smash spare
[0033] Crush the above luminous glaze frit into 325 mesh to make powder:
[0034] 3...
Embodiment 2
[0042] Example 2 The luminous parameters are measured according to DIN67510, and the luminance at the 10th minute is 450.2mcd / m 2
[0043] 1. The high-temperature luminescent glaze is composed of the following components by weight percentage:
[0044] SrAl 2 o 4 EuDy (alkaline earth aluminate) 65%, SiO 2 25%, Al 2 o 3 5%, CaO2.5%, MgO1.0%, Fe 2 o 3 0.5%;
[0045] 2. The processing technology of the above-mentioned high-temperature luminescent glaze includes the following contents:
[0046] A. Mix and grind
[0047] After mixing the components described in 1 above, place them in a ball mill for 6 hours and sieve to 325 mesh;
[0048] B. High temperature melting
[0049] Put the mixed and ground luminescent glaze on the shuttle furnace of the oxidation isolation device to burn the frit, the firing temperature is 800-1000°C, and the firing time is 3-6 hours;
[0050] C. Smash spare
[0051] The above-mentioned luminescent glaze frit is crushed into 325 mesh and ma...
PUM
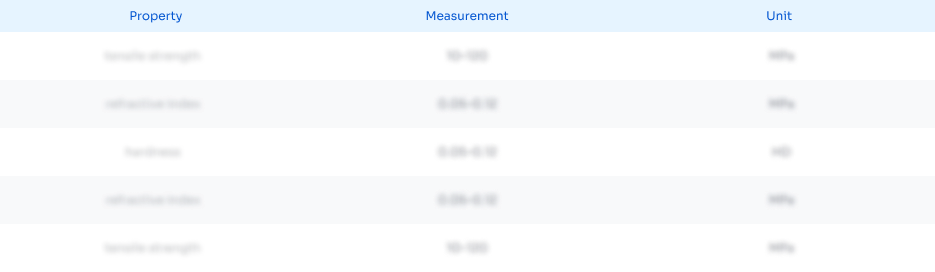
Abstract
Description
Claims
Application Information

- Generate Ideas
- Intellectual Property
- Life Sciences
- Materials
- Tech Scout
- Unparalleled Data Quality
- Higher Quality Content
- 60% Fewer Hallucinations
Browse by: Latest US Patents, China's latest patents, Technical Efficacy Thesaurus, Application Domain, Technology Topic, Popular Technical Reports.
© 2025 PatSnap. All rights reserved.Legal|Privacy policy|Modern Slavery Act Transparency Statement|Sitemap|About US| Contact US: help@patsnap.com